3 Logistics Miracles Made Possible With Real Time Data, Miracle #2: Labor Management
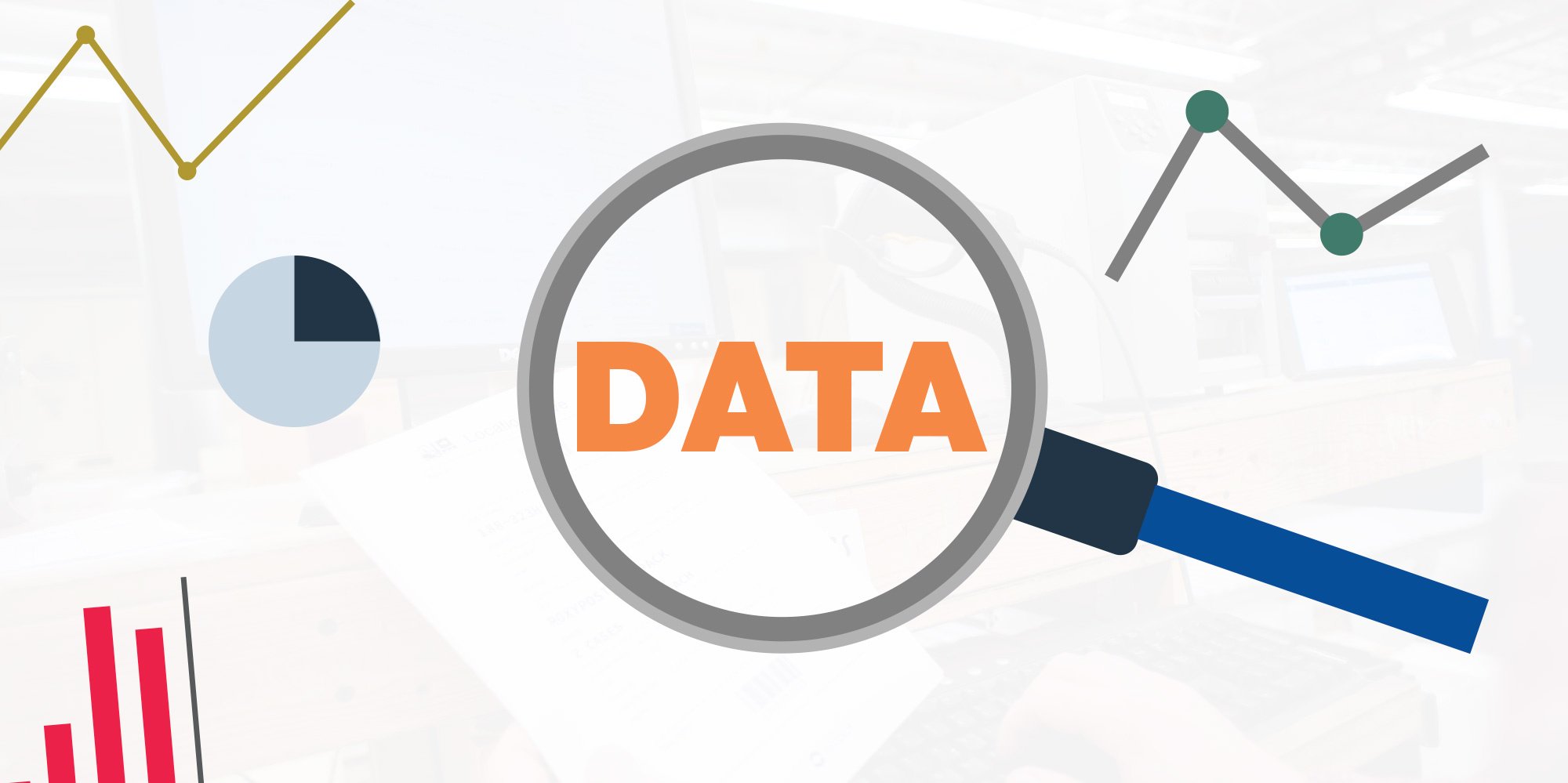
Warehousing and storage in the United States is currently a $22 billion industry which employs over 600,000 people. Add in order fulfillment, and these numbers increase to $31 billion and 660,000 employees. Since labor is one of the biggest costs in any logistics operation, efficiently managing that workforce is key to a company’s success.
The low-hanging fruit in labor cost management is in scheduling. Why? There are peaks and valleys---both in stores and online---in purchase volume. When purchasing is slow, excess labor capacity means wasted money. But businesses must also be able to deploy labor as needed when purchasing spikes. If purchases spiked one day and your warehouse did not have the workforce on hand to handle the increase in orders, it can mean unnecessary delays...and costly overtime.
These situations leave warehouse managers in a dilemma. A large labor force on the warehouse floor means the ability to absorb any peaks in demand. It also means that, when times are slow, you will be paying people to sit around. On the other hand, if you keep a “lean” labor force, you will be put in the position of needing to hire temporary workers. While this works for seasonal upticks in orders, it is not a viable strategy for shorter periods of time---daily, for example.
So how do you allocate labor so as to be as efficient as cost-effective as possible? Trick question: labor management is not a matter of how to assign labor but when. Ideally, floor managers would be made aware of potential labor shortfalls with enough advance warning to do something about them, such as bring on additional temporary labor. This way they can keep a smaller “core” workforce, augmenting it during peak times with workers hired just in time to meet the surging demand.
How Real Time Data Helps
Here’s a scenario that might be familiar: Suppose an enticing offer from the marketing department causes online sales to surge overnight. You did not expect this volume of purchases to occur so suddenly, and you know that your warehouse will be understaffed.
Now imagine that, prior to the first shift of the day, your floor manager receives an alert informing him of the sudden spike in online orders. The manager calls in additional help well before the shift begins, guaranteeing that workers can keep up with the workflow and get all items out within 24 hours.
This is an example of a push notification, which notifies one or more users of a situation or event, even when the user is not logged into a system or app. Infoplus, for example, can simultaneously send push notifications to your floor manager, warehouse supervisor, and general manager even when they are not in the Infoplus system. This allows them to receive alerts about operations-critical events.
Push notifications only work if system data is updated in real time and sent to compatible devices. It does no good, for example, to receive a quick alert regarding a shortfall...after operating hours are over, and the item has been Out of Stock all day.
So why aren’t more companies embracing real time data to enhance their labor management? In short, fear. Fear prevents companies from taking the necessary positive steps to make the flow of labor more efficient. Common fears include:
Employee Backlash. Many companies believe that labor management programs will be seen by employees as a way to cut hours, employees, or both. They ultimately fear the backlash that will happen when new systems are introduced or when last-minute changes are made because of some “alert.”
This fear is unfounded. Employees find labor management systems to be a fair way to schedule work, and they often appreciate the opportunities for extra work during busy times. (This is especially true if incentive pay is used.) Both employee morale and efficiency significantly increase.
IT Nightmares. True, if your current system does not give you real-time updates, deploying a new system can be a challenge for your IT team. A cloud-based system offers just the features needed when they are needed without a heavy IT expenditure. If that software can send alerts to multiple platforms, implementing it will be even easier.
More Work Caused by Poor Integration. Labor management should neither sit as a function by itself nor be handled with a single piece of proprietary software. When this happens, several databases will need to be coordinated, often in a batch process...which misses the point of having real time data to begin with.
When systems are not properly integrated, products become unavailable for shipment or do not ship on time, which in turn can disrupt an optimized transportation schedule.
Like customer service, labor management is a key area of logistics where real time data can have a noticeable impact on operating efficiency. In a future post, this blog will cover shipping efficiency both on the customer side and on the supplier side.