How Can Warehouse Management Software Reduce Costs For 3PLs?
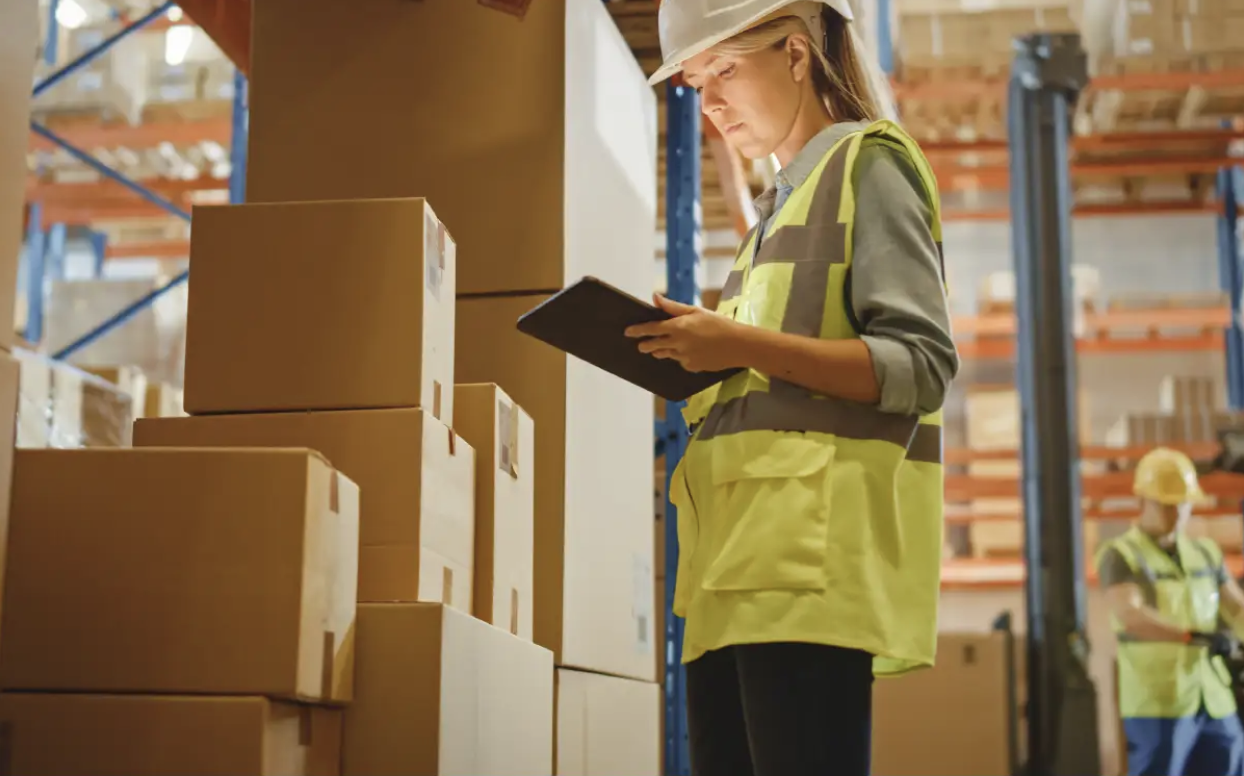
How a 3PL Warehouse Management System Drives Profitability and Customer Satisfaction
For many companies, switching from fulfilling their orders in-house to using third-party logistics (3PL) can feel like a leap of faith. They’re trusting another organization with their products, processes, and, ultimately, their customers. However, the right 3PL warehouse management system (WMS) doesn’t just improve fulfillment—it drives significant cost savings and efficiency gains.
A well-implemented WMS helps 3PLs lower labor expenses, reduce costly order errors, and optimize inventory management, all of which improve margins while maintaining top-tier customer service. The result? Happier clients, fewer operational headaches, and a stronger bottom line.
6 Ways a Warehouse Management System Helps with Reducing Costs
The secret to achieving better margins is, of course, customer satisfaction. The right Warehouse Management System Software allows 3PLs to do more for their clients with fewer resources while improving operational efficiency and reducing costs. A WMS can do this by:
Automating Warehouse Operations to Lower Labor Costs
Automating repetitive tasks, such as order routing and inventory updates, reduces the need for manual labor and minimizes costly errors. With optimized workflows, warehouses can handle higher volumes without increasing staffing expenses.
Managing Inventory to Control Operational Costs

Overstocking ties up capital, while stockouts result in rush shipping fees and lost sales. A WMS provides real-time inventory tracking, helping 3PLs maintain the right stock levels and avoid unnecessary expenses.
Improving Order Fulfillment Accuracy to Reduce Returns
Incorrect shipments lead to costly returns, reshipments, and damaged customer trust. A WMS ensures orders are picked, packed, and shipped correctly the first time, reducing waste and logistics expenses.
Eliminating Manual Errors That Lead to Expensive Mistakes
Mistakes in inventory counts, order processing, and shipment details can cause operational bottlenecks. Automation prevents costly delays and eliminates the expense of fixing avoidable errors.
Optimizing Picking and Packing to Cut Fulfillment Expenses
Inefficient picking paths and poor warehouse organization waste time and resources. A WMS optimizes warehouse layouts and automates pick paths, allowing for faster order fulfillment with minimal labor costs.
Providing Real-time Data Insights to Prevent Costly Inefficiencies
A data-driven WMS highlights inefficiencies before they escalate. By analyzing trends, 3PLs can refine operations, reduce overhead, and improve cost efficiency across the board.
Automating Warehouse Operations Allows for More Efficiency
A 3PL warehouse operates at its full potential by automating key warehouse operations and processes. It takes work to receive, store, and complete product orders. Every element of the logistics operations process and 3PL warehouse management function must be scrutinized, from every angle, to determine what you can do to improve and increase efficiency.
This is especially true if the items being received or stored are delicate, or have special storage requirements. 3PLs need to automate repeated processes if they want to grow and scale.
For example, a warehouse management system should help automate the selection of an optimum picking strategy and pick paths, organize the warehouse layout for maximum efficiency, and schedule the workforce required to complete forthcoming orders. These automations add up and, with volume, lead to significant savings.
Inventory Management Helps Control Costs
Any 3PL already understands how to move products from point A to point B, keep a log of inventory on hand, and so on. But things get more complicated when you're responsible for juggling inventories for multiple customers at once.
Effective inventory management calls for ongoing optimization to anticipate the future. Most 3PL operators wish they could look into the future to meet customer needs better and anticipate developments before they happen.
One of the greatest strategies to guarantee the best inventory management for the present and future is to have reliable and dedicated warehouse management software at your disposal.
InfoPlus’ insights tool leverages machine learning, AI, and advanced data mining to provide outputs about labor estimates based on order expectations and trends within a warehouse. It also provides outputs about the most optimal layout and picking methods based on the type of orders anticipated.
Improving Order Fulfillment Accuracy
Warehouse management software can help 3PLs improve order fulfillment accuracy, which reduces returns and customer complaints. A warehouse management system enhances order fulfillment by eliminating manual errors in order processing and inventory counts. The right WMS will eliminate errors in inventory counts, shipment data, and other areas of your operations that lead to inaccurate shipments.
In addition to reducing operating costs by reducing returns and customer complaints, warehouse management software also allows you to provide better customer service by giving customers access to real-time information about their orders at any time through mobile apps or web portals.
Optimizing Warehouse Operations
Errors in order fulfillment can lead to costly returns, wasted time, and dissatisfied customers. A WMS helps 3PLs optimize receiving, picking, and packing by reducing manual mistakes and increasing efficiency. With real-time inventory tracking and automation, a WMS ensures that every order is processed quickly and accurately.
- Receiving - The first step in order processing is ensuring the warehouse has the necessary inventory in the correct warehouse locations. Large orders may have inventory spread across multiple facilities, making real-time visibility essential. A WMS with barcoding and slotting rules ensures workers can efficiently track inventory and locate items, reducing manual errors.
- Picking - Using seamless integration with other systems, a warehouse management system can automatically send location details to pickers for fast and accurate order fulfillment. Increased efficiency in picking leads to faster order processing and improved logistics services.
- Packing - After picking, cartonization, an advanced WMS feature, selects the optimal box size and packaging material. This prevents errors in order fulfillment and minimizes waste.
According to Extensive, in 2024, only about 30% of warehouses reported taking more than 90 minutes to fulfill and ship orders.
Real-time Data Insights and Reporting
Providing detailed and customizable reporting allows third-party logistics providers to demonstrate their value to customers. A comprehensive WMS provides:
- Customizable dashboards showing real-time data on key performance indicators
- Exception reporting that highlights issues requiring immediate attention
- Trend analysis identifying opportunities for improving operational processes
- Customer portal access providing real-time visibility into inventory and orders
By leveraging these real-time insights, 3PLs can make data-driven decisions that optimize operations and drive efficiency. This not only improves service quality but also directly impacts the bottom line—leading to a strong return on investment.
WMS' Return on Investment
Investing in a warehouse management system is a strategic decision that yields a significant return on investment (ROI) for 3PLs. By reducing operational costs, increasing order fulfillment accuracy, and streamlining logistics operations, a WMS quickly pays for itself.
Enhanced real-time visibility and inventory tracking minimize lost or misplaced stock, while automation reduces labor costs. With better order management, third-party logistics providers can take on more customers without increasing overhead, boosting profitability and long-term growth.
Take Your 3PL Business to the Next Level with a User-Friendly Management System
Utilizing technology enables a 3PL to offer unique services that better support the growth of the logistics provider and its clients.
A 3PL that provides cutting-edge services will outperform its operating margins and ultimately draw more clients. A 3PL will become even leaner and more competitive by utilizing technology, supporting the bottom line's expansion. Order management using cutting-edge technology will pave the path for future success in the cutthroat world of contemporary third-party logistics. For a 3PL to develop enduring client connections, a comprehensive WMS with solid technical support is essential.
We designed our cutting-edge warehouse management system for growth. It will cut labor expenses, provide total visibility, enhance warehouse operations like order management, and boost the profitability of your 3PL. To find out more, request a demo today.