Increasing Warehouse Productivity in Critical Times
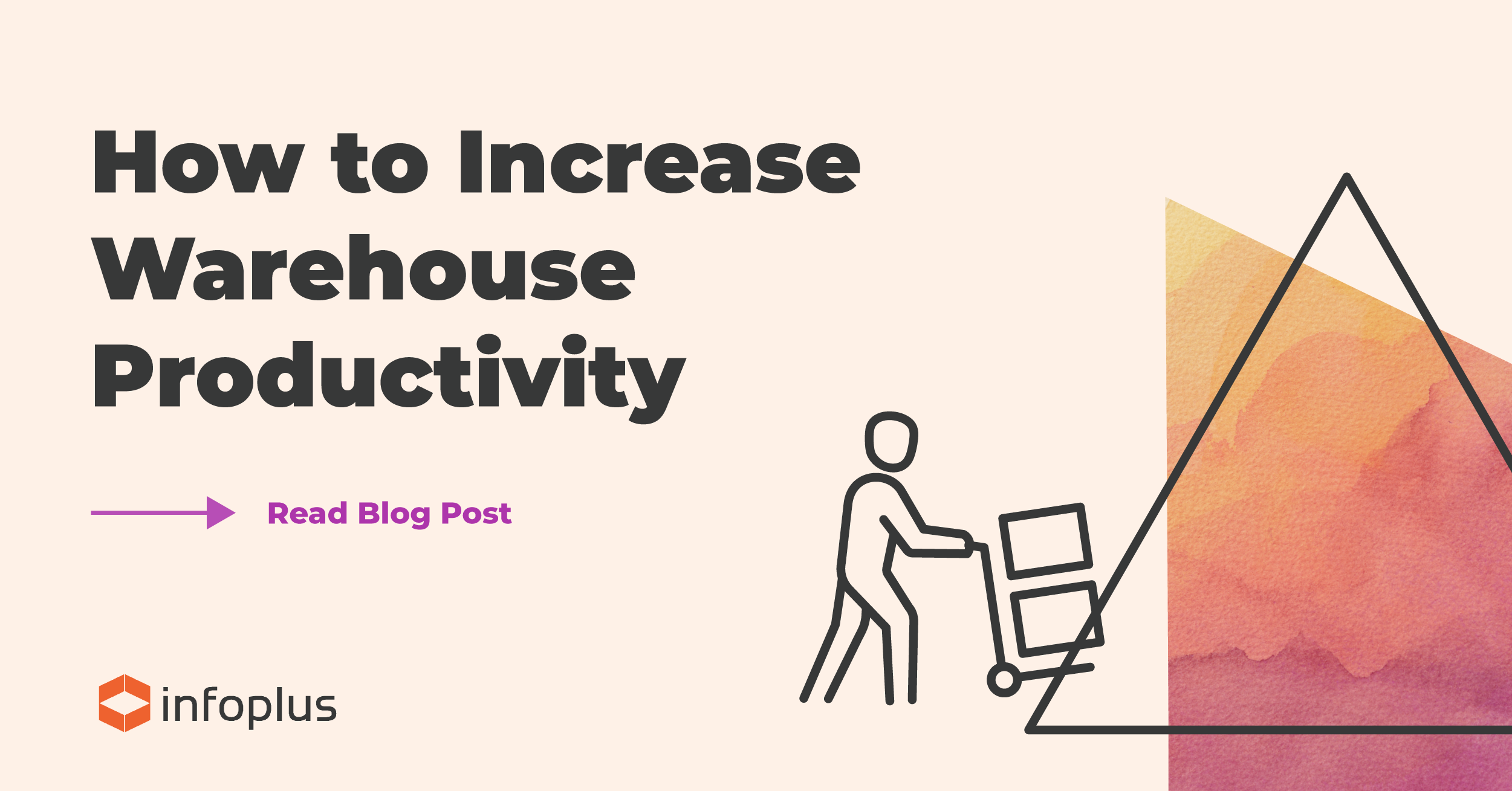
Warehouses and manufacturers can experience a sharp demand for some products during a crisis. How can you scale quickly to meet these sudden, unexpected surges in demand? It takes some preparation with regard to warehouse layout planning, automation, integration, and tracking of KPIs. So do an honest assessment: Can your warehouse management system manage these changes and handle the increased volume in critical times?
Warehouses and manufacturers can experience a sharp demand for a product during a crisis. Whether a spike in volume is the result of an isolated incident at one facility or a global emergency, the task is the same: Scale up operations to get goods out the door to buyers.
Ramping up productivity in critical times requires a balance between planning and flexibility. By taking steps to optimize operations on several fronts before an emergency, a warehouse can do more when necessary, but also be ready to pivot at a moment’s notice. In other words, prepare for the worst-case scenario...but do so with the realization that, if and when it happens, the scenario may not fit the plan. Companies that can modify their plans and switch gears quickly and smoothly will have a better chance of coping successfully with whatever comes its way.
A spike in volume often comes along with other logistical challenges. As outlined in Thriving Despite Chaos: Warehouse Management in Critical Times, the need to increase productivity can be combined with staff shortages, limited resources, and adjusting to a remote work environment, all while ensuring workers’ wellbeing. As a company strives to increase volume, it must be conscious of how all of these components work together toward the eventual outcome.
Essential vs. Non-Essential Products
Sometimes the demand for a product is obvious. Food, toiletries, safety equipment, and medicine will be needed no matter what. Or, it might be essential to the specific crisis at hand. For example, the demand for ventilators skyrocketed during the 2020 COVID-19 pandemic. Makers of essential items, as well as the companies that warehouse, ship, and sell them, will feel intense pressure to keep the flow of goods moving into the marketplace. When an item is of particular importance, its maker may even be compelled by the Defense Production Act of 1950 to prioritize or allocate items on behalf of the federal government.
Even if items are not necessary to the situation, they might still experience a surge in demand. These kinds of products are hard to predict without data, though the logic makes sense when you think about it. Take online orders of puzzles and games, for example, which surged with the 2020 quarantine as families found themselves house-bound. Or another example is Walmart shipping additional strawberry PopTarts to their stores when a hurricane is predicted.
Indeed, these sudden surges in volume are much like a seasonal spike, only with the added element of surprise. While there might be some warning (for example hurricane season or when conditions are right for wildfires) the timing and severity of the crisis might be completely unpredictable.
Human behavior can be unpredictable, too. A perceived shortage of a common item can incite panic buying and hoarding. Whatever the cause, without planning ahead, companies will have a hard time keeping up with demand. Here’s what needs to be done to respond swiftly to an emergency and get their products to consumers.
Optimized Warehouse Layout
The most productive warehouses are those that have been optimized for efficiency in every area of operation. The layout of the warehouse plays a huge role in this. If the space is not well-organized it will not run efficiently in normal circumstances, let alone during a time of high demand.
Organization is essential in every part of the warehouse layout, from the point materials are received, until they head out to customers, and everywhere in between. Nail the layout of the warehouse, and it will show in your overall efficiency, and how easily you can scale should you need to.
A good layout has defined areas for each part of the operation. These may differ depending on whether the warehouse is small, mid-sized, or large, but the concept is the same. Typical areas will include receiving, storage, picking, value-added area, packing, wholesale staging, and shipping. Ideally, there will also be some vacant space for room to grow. In critical times, there may be a need for additional inspections or kitting of products. If a company is already bursting at the seams, these will be difficult, if not impossible, to manage.
Each area should be mapped out to move products through the warehouse in the most direct manner. This means keeping the number of touches and steps to a minimum and avoiding bottlenecks, crossing paths, and backtracking. This can be accomplished with:
- Clear receiving procedures
- Storage areas that are clearly labeled and easy to navigate
- Logical and well-defined pickpaths
- Streamlined and accurate packing and shipping
Poor, chaotic layouts make a warehouse move products slower and with a greater chance of errors and accidents. For example, failure to use a forward picking area means unnecessary trips to and from storage. A bad labelling system will lead to picking errors. Disorganized pickpaths will have pickers getting in each other's way. These problems prevent a company from running at its full potential. Chances of being able to scale to meet a sudden surge in demand are slim.
By designing a warehouse layout that is efficient and orderly, you are creating an environment that can work at capacity on a regular basis. When an emergency happens, you can speed up operations without wasting valuable time fixing and rearranging the floorplan to fix what’s wrong.
Investments in Automation, Integration, and WMS
The value of automation and integration is crystal clear when a manufacturer or warehouse has to increase productivity. Even on a small scale, automated solutions make tasks faster, safer, and more accurate. A simple conveyor belt, a machine to build or break down boxes, or a scale that automatically calculates dimensional weight are basic automations that can have big impact.
Integration goes hand-in-hand with automation, allowing all parts of the operation to communicate and work together, enhancing efficiency even more. Part of a crisis preparation plan should be a close examination of operations and implementing automation and integration wherever possible.
It is important to be proactive when looking into the elimination of manual methods. Finding the right tool for the task at hand, installing it, and training staff on how to use it, all take time. It is doubtful that a manager will have the luxury to implement a new device during an emergency.
Managers should work to eliminate some common mistakes like underutilizing machines, or keeping up old manual routines. For example, an employee may still keep using a written spreadsheet rather than trusting the data provided by the software. These habits can seriously hamper productivity should a crisis occur. It is best to break them before it’s too late.
In critical times, warehouse managers need to make data-driven decisions. Flexible, customizable warehouse management software makes that possible. Having real-time analytics to show the big picture makes for better efficiency overall and will make it possible to ramp-up or pivot when necessary.
During a spike in volume, there will be an influx of materials into receiving. Nimble receiving software will show the best way to track, unpack, and store products fast.
On the other end of the warehouse, packing and shipping will be working overtime to keep pace getting the increased orders out the door. Robust shipping software will be essential in initiating, coordinating, and tracking all of those additional deliveries.
Real-time inventory data becomes critical to fulfilling orders. WMS can also determine the best picking methods and pick paths to speed things up. It will signal when it’s time to bring in additional staff or switch to a different vendor or shipping company if the usual supply chain is overwhelmed.
Paying Attention to KPIs
Without key performance indicators, sound data-driven decision-making is impossible. KPIs are always important, but in this new normal some may become less important while others take on new relevance. For example, Carrying Cost of Inventory (as it’s going out as quickly as it’s coming in) or Revenue Per Employee (profits may not be as relevant in an all-hands-on-deck type emergency) may be replaced by Order Lead Time or Inventory Turnover in the minds of management.
Special attention will need to be paid to KPIs that could signal not just an increase in backorders, but an actual shortage of a certain product. Automatic alerts can let a manager know when certain KPIs are approaching, reached, or missed. They will be able to take action immediately, rather than waiting until they have time to run a report—which could be too late. Extra time will be in short supply, so KPIs dealing with accuracy will be important to reducing returns. Meanwhile, quality control data remains important no matter what is happening.
Keeping an eye on KPIs will allow managers to make crucial decisions during critical times. It is important to have a WMS that provides many different indicators that not only provide a clear view of operations but can be modified quickly as needs change.
A Production Checklist for Critical Times
In a crisis, urgent demand for a product will push a business to its limit. How well they handle the chaotic and fast-paced environment can either make them or break them. Preparing for critical times before they happen is key, as is the flexibility to pivot or tweak production processes as situations change.
Here are the areas to look at and address now, to be more nimble in the face of an emergency that causes a spike in volume:
- Model a plan for critical times after existing plans for seasonal spikes in volume. With some modification what works during a busy season can work in an emergency.
- Make sure the warehouse layout is designed for optimum efficiency. Make changes now to anything that causes bottlenecks or wasted steps.
- Automate wherever necessary, especially in areas where speed and accuracy are lacking. Be sure to use all available features of automated solutions, and do away with unnecessary or redundant manual tasks.
- Make sure all areas of operations are “talking” to each other by integrating systems both internally and with vendors and shippers.
- Invest in a WMS that is customizable and has the capacity to grow with your business.
- Know your KPIs and their implications. Set up alerts to indicate when action is needed. Use them to make well-informed data-driven decisions.
True, it’s not possible to prepare for every eventuality. But managers who continually strive to improve overall operations under normal conditions will fare much better than those who are constantly putting out fires. It will play a big part in which companies make it through a crisis.