7 Time Sucks in Your Logistics Operations
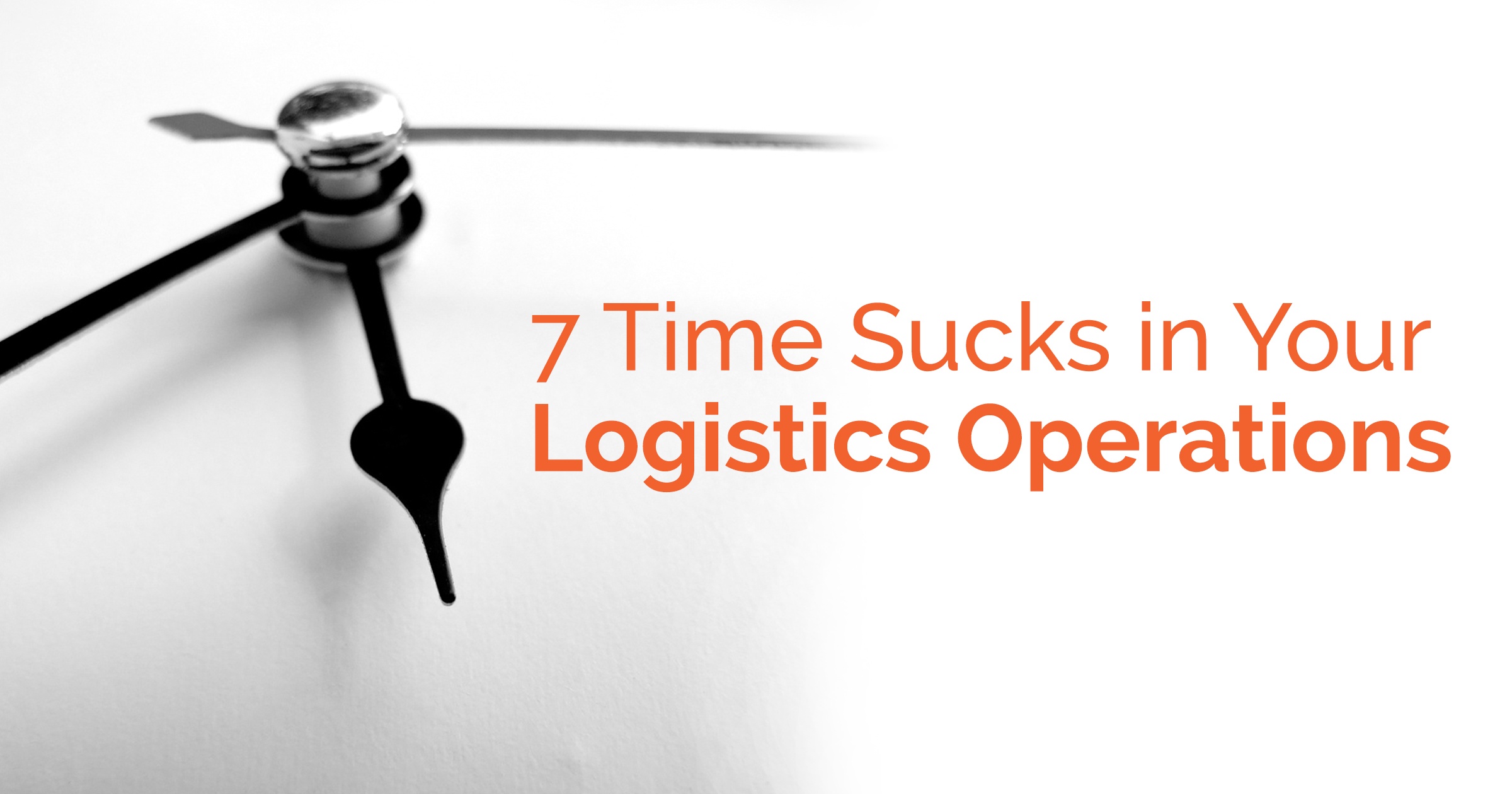
(and What to Do with Your Newfound Time)
If there were ever a first law of business, that law would probably be “Time is Money.” Investing time on activities that pay off, now or in the future, makes for a viable, competitive business. Time sucks, like the ones experts have uncovered in warehouse and logistics operations, do not.Perhaps more amazing is that many of these time sucks have little to do with traditional “lean” operations on the warehouse floor (waste in material, movement, and so on). While managers and professionals have done a good job over the past decade waging a slow war against wasted time there, they have been largely blind to practices that waste their own time. This has caused inefficiency, lost opportunity, and stress. It’s time that these “hidden” time sucks were highlighted, too.
Manually updating sales, accounting software
It is truly surprising how many warehouses and distribution centers have the latest barcode scanners and warehouse management software, but fail to properly integrate those technologies with other key systems, like sales and accounting software. Indeed, many companies end up exporting and importing data manually—or even doing the updates by hand.
Not only are manual updates time consuming and potentially stressful, but they open the door to human error. Catching and fixing those errors can waste even more time. Having integrated systems, on the other hand, allows systems to update each other automatically, in real time.
Getting data updates
Sales and accounting software are not the only points at which real-time data is needed. Having up-to-the-second updates can improve delivery times, simplify labor management, and greatly enhance customer service.
Without real-time data, much time is spent transferring, checking, and rechecking data. These inefficiencies add up—sometimes to the point where a dedicated full-time position is needed simply to manage the massive databases and compose needed reports.
Waiting for stock replenishment
Orders from suppliers do not arrive instantaneously at your loading dock. A strong purchasing department knows this and makes arrangements to put orders in motion well before stock levels reach empty.
Of course, this is always something of a guessing game. Without an up-to-date, accurate accounting of stock levels and purchase velocity, organizations run the risk of buying stock too soon (tying up capital and warehouse space) or, as is more often the case, buying stock too late (which creates back orders).
And while a warehouse waits for that stock to be replenished, its workforce and assets sit idle...as does the warehouse’s ability to collect useful data.
Waiting for approvals
Even when things are moving smoothly and there are no exceptions to standard procedures, there are chains of approval that might be needed to do things—things like preparing large orders, replenishing stock, purchasing packing materials, adjusting schedules, and so on. Approvals are definitely needed when things are outside of the norm (special orders or procedures, for example).
All too often, a warehouse will seize up, simply because some piece of paper is waiting for an executive signature. Either the executive is not alerted to the need for his or her approval, or is simply busy with other issues (see putting out fires, below). Ironically, the more often people need to wait for approvals, the more problems it causes, and thus there are more problems for management to solve. It can quickly become a vicious cycle, a merry-go-round where managers and employees alike either check out and disengage, or burn-out with the stress.
Managing labor flow
Factoring order fulfillment jobs, the warehousing and storage industry in the United States alone employs more than 660,000 people. While many of these workers are full-time, year-round employees, many are part-time or seasonal workers who put in their hours only during peak order times.
Managing all those workers and their schedules is a huge administrative task—one that frequently cuts into managers’ time. Mismanaged labor ends up being a huge time suck for warehouses as well: When there are not enough workers, everyone is stretched thin (including management). When there are too many workers, management has to find additional non-revenue-generating tasks for the excess workers, or else get embroiled in debates about who goes home and who stays.
Wayward picking paths
Wayward picking paths affect workers on the floor more so than management. Still, management decisions are often the root cause of these wayward paths, and so management needs to pay attention to time wasted by bad practices.
For example: Suppose a good-sized order is placed by a regular business client. The order contains 50 items. These 50 items are located across five different areas in the warehouse. Think of what would happen if items were picked in alphabetical order by product name. That might be a natural way to organize a packing list or invoice, but it creates a very inefficient pick and pack process: The picker might travel, for example, to area 1, then to 3, back to 1, on to 2, then 4, then 3 again...so on and so forth. Why? Because most warehouses are simply not organized in alphabetical order by product name.
Picking that 50-item order this way could easily take the better part of a day. If, however, the picking list were arranged by item area and location, the picker could select all the items in area 1 before moving on to area 2, all the items in area 2 before moving on to 3, etc. Now that same order takes only a couple of hours to pick and pack.
In fact, a study conducted by Dematic found that simply optimizing pick paths typically increased pick speed by 10 to 18 percent by minimizing the time required for finding items, travel within the warehouse, and other support activities.
Putting out (metaphorical) fires
Nothing gets in the way of strategy more often than the need to fix things. Misshipped or mishandled orders, incorrect inventory levels, improper placement and storage of items, recalls, returns, “dead” stock, mixed-up shipping and receiving, bottlenecks on the packing floor, irate customers, vendors who don’t deliver…the list goes on. Outside of actual emergencies (fires, natural disasters, and the like), small problems like these put the biggest dent in uptime for your warehouse operations. And they all require the intervention of management to straighten out the problem, adding to their workload and stress levels.
Of course, problems like these never go away. That’s the nature of any human enterprise. But they can be effectively minimized. To do this, executives need to:
- Receive alerts when something falls outside normal operating parameters. If something is out of the norm, this fact needs to be registered and reported to the appropriate parties. Management by exception is a good way to do this.
- Base both alerts and reports on real time data. Naturally, alerts should be timely. Having real-time data for reports is a good idea as well, because it empowers decision-makers to anticipate problems before they happen.
- Integrate and automate. Integrating systems through APIs can introduce a number of efficiencies while allowing an unprecedented level of customization. Automating data workflows reduces the amount of human error and protects against failures and bottlenecks.
What Will You Do With Your Newfound Time?
Nobody wants wasted time. But there is an even more powerful argument to be made for taking positive action to eliminate these time sucks. Each and every one gets in the way of more important strategic activities that can actually grow your business.
Imagine: One director of operations has a good warehouse with a good workforce but finds himself having to handle a number of mundane daily tasks: data transfer, database hygiene, labor management, building reports, and so on. These tasks themselves are constantly interrupted because of the need to put out fires—those small problems that need to be attended to and that occur randomly throughout the day.
When does this person have time to sit back, read, analyze, and strategize? When can he search for solutions to common challenges? How can he plan growth?
Now picture that same director of operations in a situation where most of those daily tasks have been automated. No longer does he have to spend hours with data transfer, database hygiene, labor management…Furthermore, those automated operations mean fewer errors on the part of warehouse staff, and so fewer fires to put out. The director now has stretches of time that can be spent analyzing daily and weekly reports instead of building them, using the data to get insights on direction for the business, researching solutions, and finding further ways to boost productivity and plan for the future.
Isn’t it worth it to be the director in that second scenario? If so, start by asking yourself this question:
What exactly are your time sucks?