17 Practical Ways to Prepare Your Warehouse for the 2022 Holiday Rush
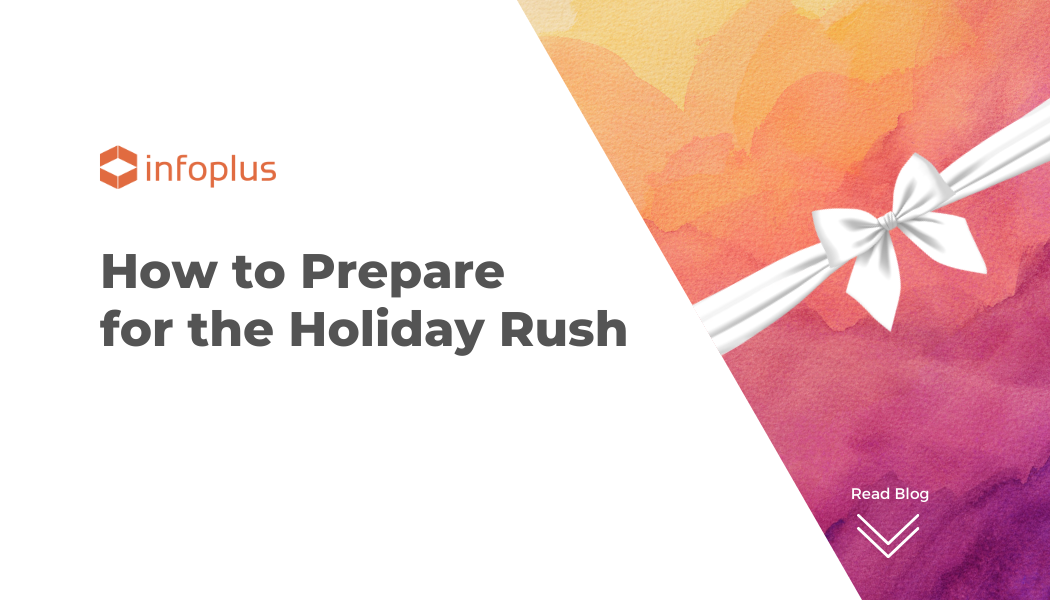
The holidays are usually a time for joy and relaxation, but when you run a warehouse, they are both exhilarating and exhausting. To prepare for the sudden increase in order volume and the urgency of shipping orders on time, There are things you can do now to prepare your warehouse for the influx of order traffic.
2021 is set to be a record year for online orders during the Holidays. The Washington Post even noted that “the pandemic is haunting the global supply chain and, by extension, shoppers.” To set yourself and your business up for success for what is likely a non-predictable season, consider some of these actionable steps ahead of the rush.
Planning for the Holiday rush means looking into all the areas of your warehouse that might need extra support or extra supplies before the increase in volume surprises your team. Here’s some advice from warehousing experts for how to get ready:
17 Measures for a Successful Warehouse
During the 2021 Holiday Rush
- Add more pack stations to handle the increase in orders and space them out among frequently ordered items
There are times when pickers can bring back product to pack stations faster than packers can package and label packages. To alleviate this and the potential bottleneck of a pack station, consider adding one or more additional temporary pack stations during your busy times. Space these pack stations out near high volume forward locations. - Check item activity and relocate high moving items to eye level pick locations and close to packing stations
Do an audit of what items are selling fast and what items you expect to sell in higher volume around the holidays. Move these items to an easily accessible location for pickers. This can be an additional or swapped out forward location or moving them down from a hard to reach location to one that is eye level or lower. - Make sure your Replenishment plans are set up correctly and your staff knows how to perform a Replenishment
Replenishments plans are crucial to ensuring that product is ready and available to fulfill orders. Checking all of the currently set up replenishments will ensure that product is regularly being stocked. Educate your staff on the procedures for performing replenishments. - Create a schedule to continually check pack stations often to ensure supplies are properly stocked at all times
Keeping pack station supplies in stock is critical especially when packaging volume is particularly high. Plan for the rush and pre-order packing supplies in order to prevent supplemental packaging, or delayed order fulfillment because you are short on tape, labels, filler(dunnage), or packaging. Specifically, review the different size packaging that you have in stock, and make sure that your best-sellers are not going out in oversized packages.
The worst-case scenario for a warehouse is for an order to be ready to go at the packing station, but you ran out of boxes… or printer ink… or labels….or tape, etc. This will grind your operations to a halt, frustrate your employees, and become a huge barrier to success. To avoid this from happening, make sure you tally up the supplies you currently have and pre-order what you expect to go through ahead of the holiday rush. - Assign a specific location for any ‘problem orders’ (i.e. orders in error, orders not able to complete)
Occasionally, orders that are partial, problematic, or errant can show up at the packing station. Designate and clearly label an area of the warehouse where these orders can be taken off the line and placed for review and correction. This will save on the backlog, and separate the orders that need special attention from the orders that are ready to go. - Assign a specific location for damaged or errantly picked items
Warehouses can sometimes get alerts on products that need to be pulled out of availability. Or sometimes it is discovered that an entire lot is defective or damaged. Designate and clearly label an area of the warehouse where these items can be brought for review and potentially recalled. - Look for any patterns on past orders (place items typically ordered together in close proximity)
During the holiday rush often specific items get ordered together, or are part of special holiday sales. Do an audit of the most commonly grouped items and consider placing them near each other for fulfillment, this has the potential to save your pickers extra steps and time when orders are being picked. - Check equipment and make sure everything functions properly before demand increases
Weeks before the major rush it is very important to schedule equipment and systems checks leading into the busiest times. Nothing is worse than having a forklift, printer, or walkie-talkie go down in the middle of the busiest week of the year. If you plan at least three weeks ahead to check all systems, you will have enough time to have maintenance completed on any printers, forklifts or hard-to-schedule maintenance equipment.
Printers can cause the biggest backup in the warehouse, make sure that the scheduled maintenance is done, and the ink and paper are ready.
- Consolidate pallets
If there are multiple partial pallets taking up space in the warehouse, (especially in prime locations) combining partial skids will free up space and create more flexibility. High moving SKUs may have a pallet for replenishment that can now be moved to a more productive and efficient location that may have previously been occupied by a partial pallet.
This also serves to conserve the number of locations that pickers and the WMS need to identify to fulfill orders.
- Maximize space by considering vertical storage options
This is not suggesting double stacking skids. This is having bays and racks that can separate the items and keep the warehouse organized. If time and investment permits, getting these placed before the holiday rush will move the lesser ordered items vertically upwards in your warehouse, and keep the most trafficked items low where every picker can access them quickly. - Analyze last holiday season and determine staffing and inventory needs and plan ahead
Assuming that every year will be busier than the last is safe practice. So, analyze the staffing you needed last year, and consider that you may need more. Plan to hire seasonal workers if needed. If the demand spikes, look into staffing agencies for temporary workers; these workers are trainable and easy to dismiss if the demand turns out to be less than you were planning for.
Pro Tip: Make sure you have comprehensive easy-to-access and easy-to-digest training resources available for any seasonal or new hires that come on during this time. - Analyze pick paths and determine optimal routes
Reorganizing your items or location addresses can really change the number of steps that your warehouse picker is taking. The goal is to get your pickers to take the least amount of steps possible. There are several ways to achieve that:
- Pick by zone
- Pick by location
- Move items to locations that will optimize picker traffic
- Change the location addresses(naming conventions) to create clear paths for popular order picking. (Ex. Locations A1, AA1 are too similar and can cause pinballing around the warehouse)
- Analyze logistical needs and touch base with reps- may require more carrier pickups, possible need for trailers
Package volume may be much larger than usual. For warehouses that have daily pickups with carriers (UPS/FedEx/etc), it would be wise to contact the account representatives for these carriers and discuss options for handling the increased package volume. Possibly schedule multiple package pickups per day.
Another option is to see if your carriers would be willing to drop off a trailer at your dock and once it is full, you can have the carrier pick up the full trailer and drop another empty one if necessary.
Note: USPS is generally not as responsive to customer queries as UPS or FedEx, so try to communicate with the carrier in advance if you know that you will have increased volume for USPS to work something out.
For special items that require unique permits and certificates (alcohol, hazmat, etc.), plan ahead and make sure that all the necessary paperwork is ready.
- Ensure all freight accounts are up to date, no holds in place, payment up to date, etc.
As well as the standard carriers (UPS, FedEx, USPS) make sure that all of your freight relationships are in good standing, and that there is nothing that could prohibit a pickup for any reason. In particular, if you are shipping out using full truckload services, there is no such thing as too much communication. The space taken up in your warehouse by fulfilled orders waiting to be picked up can cause other things to backup as well. - Meet with staff and discuss any obstacles encountered last holiday and brainstorm solutions
Consider having a pre-holiday meeting with the staff, especially the ones who were present during the last holiday rush. Take the time to share ideas about what did work and what didn't work during the previous holiday season. This also gives you an opportunity to get them to share their concerns and worries; voicing those is often a good way to get buy-in for the solutions provided. This can also provide an opportunity to team up experienced workers with the less experienced workers to provide better training for your temp and seasonal staff. - Investigate and resolve inventory discrepancies
At the least, provide cycle counts on your highest trafficked items right before your busiest week of the year. If you have the staffing to do it, and the inventory is easy to review, perform a manual count with items that are expected to have increased activity at least two weeks before the rush begins. This can resolve inventory discrepancies that can be crippling to a fulfillment process. - If using seasonal workers, create clear and concise instructions of responsibilities per role
Often during busy seasons, warehouses will utilize seasonal workers to meet staffing needs. These employees may not be familiar with the warehouse's processes or workflow. To minimize confusion and help maintain productivity, all responsibilities associated with their role needs to be clearly explained.
Another tip is to schedule out 30 or 60 minutes with the seasonal employees for a Q&A session to ensure everyone is on the same page and has clear directives.