5 Red Flags for Your Warehouse and Shipping Operations During the Holiday Season (OND)
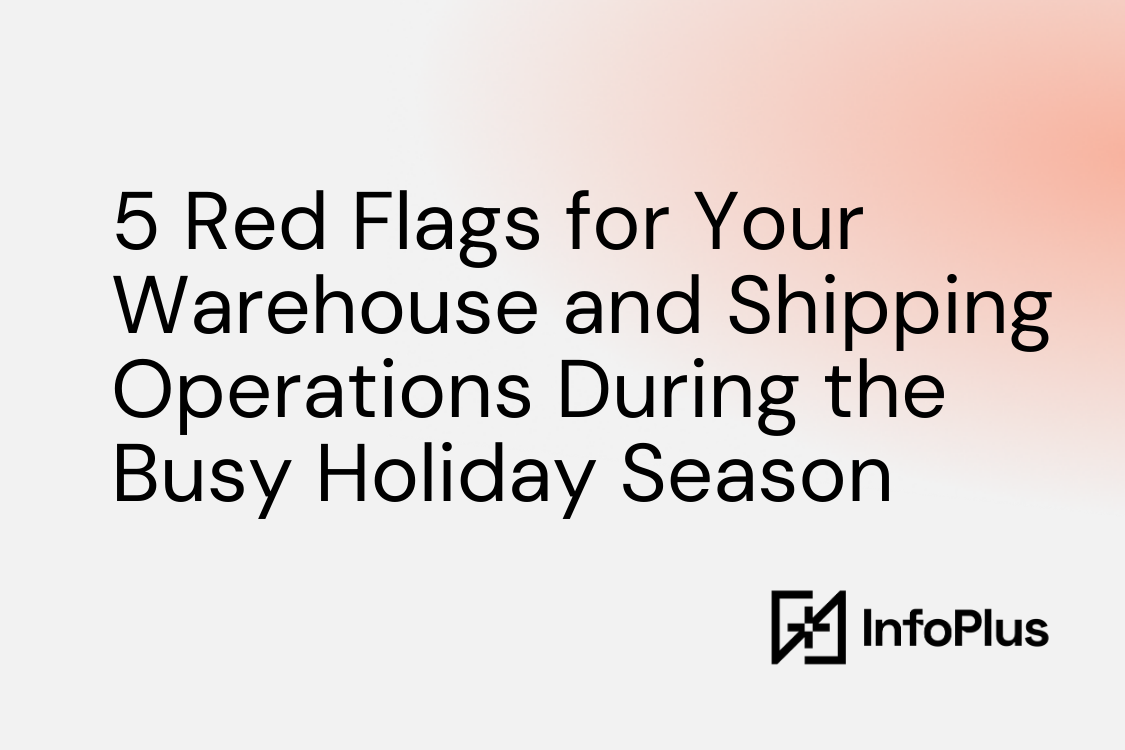
My friend’s dad had an old car with a serious defect. The defect wasn’t obvious while driving around town—in fact, you could drive it for months and not notice, if all you did were milk runs and kid carpools. But if you took that car out on the highway, you’d notice it start to rattle and shake. By the time you got to highway speeds, the thing felt as if it would vibrate itself into pieces.
Warehouses and distribution centers tend to be the same way. They appear to run smoothly while order velocity is slow and steady. But as soon as things speed up, the defects and inefficiencies in them become apparent. Do nothing about them, and you risk having the whole operation slowly tear itself apart.
This happens all-too-often during the busy holiday season, or OND (short for “October, November, December”—the three busiest months of the shipping calendar). Orders increase substantially during this time, and shippers are hard-pressed to keep items flowing out the door in time for delivery. Warehouse and shipping docks that had been running smoothly all year suddenly encounter problems once orders hit a certain velocity, and warehouse managers find themselves putting out fires on a daily basis.
In short, OND is the time of year when warehouses and logistics operations are “stress tested.” Inefficiencies and problems are most likely to reveal themselves at this time. A savvy warehouse owner or manager will keep an eye out for these five red flags that indicate something is wrong before operations get behind and SLAs are no longer being met.
#1 Overflowing Packing and Shipping Areas
Any area of your warehouse can become a bottleneck, but packing and shipping stations are especially vulnerable, simply because there are a number of manual steps that must be completed (weighing, packing, inspection, wrapping, etc.). A bottleneck here tends to compound problems, as clutter not only slows down the work that needs to get done, but increases the chance of errors.
If orders are building up in your packing and shipping areas, it might be time to rethink their design, or to add additional areas to handle the seasonal spike (or better yet, both). It might also pay to move some personnel from picking activities to packing and shipping.
#2 Not Enough Labor on Hand
Seasonal spikes in demand are predictable, and so the need for added labor should be predictable, too. If there aren’t enough hands on deck to process orders accurately and in a timely fashion, your warehouse workers and managers will let you know.
Some warehouses resist adding seasonal labor, thinking that doing so will help control costs. This is almost never the case: Not having the needed labor on hand can lead to slowdowns, bottlenecks, and unnecessary overtime pay for regular workers. And when those SLAs aren’t met, it hits the bottom line come next year.
The trick to optimizing labor spend is in using data to predict when the spike will come, and then proactively scheduling your workers to handle the volume. Optimizing warehouse setup and picking methodologies then lets you squeeze even more productivity out of your workforce.
#3 Out-of-stock on Popular Items
Seasonal demand isn’t just the demand for labor. Certain products sell vastly better during OND as well. Gift items (gadgets, perfume, gift baskets, and so on), wine, and winter accessories tend to sell really well during OND. Water wings and charcoal grills—less so.
In addition to seasonal variation, there are popular trends as well. The new iPhone and its accessories will be hot one year, but maybe not the next. Cardigans might be out of fashion this OND, but might suddenly be the “in” thing next season.
Every shipper should try to predict what items will be popular in a given shipping season and prepare to ship them at an increased velocity. If you notice these items running out, something has gone wrong. For example, did you not order enough to meet demand until the next shipment can arrive? Or did you not get a “Low Stock” alert when the SKU was almost depleted?
If there is an issue in your inventory management, it will show up in your popular items first, so watch these like a hawk.
#4 Manual Paperwork in Your Workflow at Key Points
Are the people at your receiving dock still entering order information manually into your system? What about your packers—are they entering in their order fulfillment information? Are cycle counts still being done by someone walking around with a clipboard?
Those manual processes might be OK when things are not busy, but during OND, they will become serious bottlenecks. A fully modern warehouse should be employing barcode scanners and a centralized WMS to track inventory from loading dock to shipping dock. If you notice anyone entering data manually, you should immediately ask: What value is that step adding? And how can it be automated and integrated with our digital systems?
#5 People Take Safety Shortcuts
This is perhaps the biggest red flag—people that are so rushed in their work that they begin to skirt basic safety precautions. This can include not using safety equipment (such as protective gloves or back braces), careless operations of forklifts and other moving devices, failure to inspect equipment regularly, or simply moving too fast through areas crowded with people and products.
People often take shortcuts not because they do not know better, but because they feel rushed and reason to themselves “it won’t hurt to flaunt precautions this one time.” But as we all know, just one time is all it takes for a serious accident.
And even if a serious accident doesn’t occur, that lackadaisical attitude can have other effects—for example, increased breakage rates or increased errors on orders picked.
Forklifts are one of the most common causes of accidents in the US. Industry statistics in the US cite a 90% probability of a forklift being involved in a serious injury or fatality accident over its useful lifetime. The Occupational Safety & Health Administration estimates that forklifts account for 61,800 minor injuries, 34,900 serious injuries, and 85 forklift-related deaths every year (OSHA).
How to Stay Vigilant During OND
The busy holiday season means that everyone will be working hard to get orders out the door on time. But there is a marked difference between a well-prepared, well-equipped team stepping up their productivity, and a team that is stressed to the max and creating more problems as they work. The job of leadership is to keep an eye on operations, looking for “stress cracks” in the foundation that indicate trouble brewing.
Does this mean watching your employees like hawks? Not at all. Rather, it means having the technology and resources to make that kind of tracking part of the workflow to begin with. For example:
- Inventory should be tracked using barcodes and barcode readers as soon as it hits the loading dock.
- Pickers should use similar guns to indicate their activity, updating your system so that you have an accurate count of each SKU.
- When a SKU gets too low to support stock levels given that SKU’s order velocity, the system should generate an alert so that your purchasing manager can order more.
- Pick accuracy rates and rates of return should give you an idea of how many errors are being committed manually.
- Pick and pack rates should be measured, giving you an idea of where to allocate your labor.
There are a number of warehouse indicators you can track with the right technology. The idea is to pick a few key ones and monitor them so you can make improvements. But until then, you can still rely on careful observations, like those above.
And when you are ready to invest in a WMS that can give you the right insights so you can tackle your next busy OND season, contact us.