7 Steps to Avoid Backorders and Optimize Stock Levels
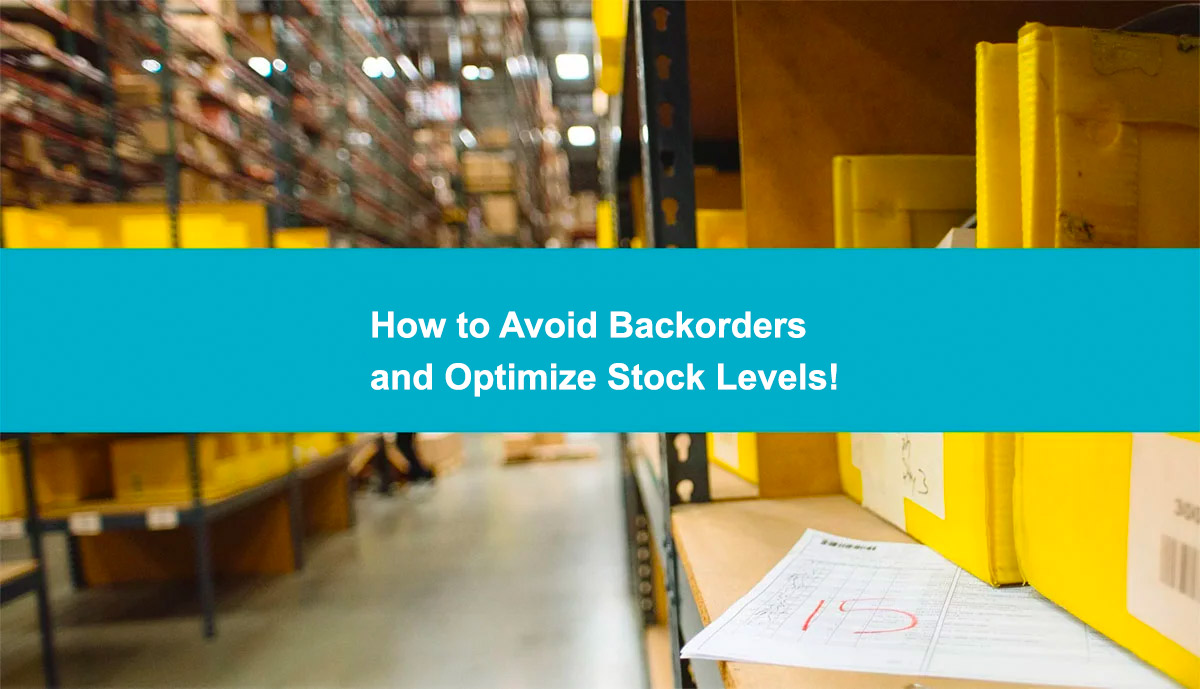
Backorders have existed as long as supply lines and logistics. But with increasing competition in and from eCommerce companies, maintaining stock to avoid backorders is an important part of meeting customer expectations. Enter modern warehouse management solutions.
What Does “Backorder” Mean? What is Backorder?
A backorder is an order (or part of an order) waiting to be filled, usually because the merchant in question does not have that item currently stocked in the warehouse. By some estimates, 34% of all companies have shipped an item late because of backorders.
In the past, whenever a merchant ran out of a given SKU, the company would simply issue a backorder while they purchased or manufactured more items. Customers would then wait for the item, taking the delay as a fact of life.
Those days are long gone.
Today, modern warehouses are tracking both inventory levels and item velocity, making precise predictions about backorders, out-of-stock SKUs, and low stock levels. They use that information to trigger action items so that inventory never “runs dry.” In effect, predictive algorithms, automation, and modern warehouse management tools have basically eliminated backorders for many merchants.
And that is a great thing when it comes to customer experience.
How to Avoid Backorders and Optimize Stock Levels
When a company, particularly an eCommerce company, takes a backorder, they are saddling the customer with a delay. That delay can last days or even weeks. (For some concrete examples of the problems that backorders create, see our article on The First Rule of Inventory).
Backorders are bad, plain and simple. But how do you avoid backorders and optimize your stock levels?
-
Get Real-Time Data on Your Stock Levels
The first step to avoiding backorder situations is getting a system in place to accurately track inventory in as close to real-time as possible. Integrating your warehouse inventory systems with the latest scanner technology and getting real-time alerts will help you avoid stock and backorder issues. There cannot be a whole day’s delay, between when you actually run out of items and when you discover this fact. -
Get Real-Time Data on Item Velocity
It is not enough to know stock levels in your warehouse; you have to know how fast items are moving, too. It’s part of your inventory needs projections. For example, you might have less than 25% of your original stock of an item, but if that item is moving slowly, you might not have to reorder for some time. Conversely, a fast-moving item might need to be ordered while you still have many items in your warehouse inventory to prevent a backorder situation. Thus, velocity matters more than absolute levels. -
Have the System Make Predictions
Once you know how quickly items are moving, you should be able to forecast when they will be depleted (also called needs projection) and compare this timeline to how long it takes to restock. For example, suppose it takes about three weeks to get a restock of item X from your supplier. You now know to set up a trigger in the system so that when the inventory in your warehouse reaches the point where there roughly a month’s volume remains, a reorder is automatically triggered. The new items should arrive just in time to avoid having to flag orders as backorders. -
Create a System that Triggers Appropriate Actions
Knowing when you are going to run out of stock is not enough. Have the alert trigger the appropriate reaction: a reorder from a vendor or an internal work order. Build in time for receiving, quality control, and put-away as well. Actions should also trigger if items are not received within the expected time frame. -
Keep All Order Channels Updated
All of your order channels and shopping carts will need to be kept aware of your inventory levels. This not only signals item availability to the customer, but it can also spur them to buy now; “Only 4 remaining in stock…” instills a sense of urgency. The whole process can be automated if you have the right order channel integration with a wms. -
Have a Back-Up Plan
Sometimes, even with the best of intentions and the most careful plans, you run out of inventory. There are many causes: A vendor could go bankrupt or have its shipments tied up in customs. Shipments to your facility could be delayed due to weather. Or an item might no longer be manufactured by your usual source, forcing you to find another. For all these kinds of situations, it pays to have a backup plan—for example, using a back-in-stock alert plugin.
Importance of Eliminating Backorders?
Backorders have been the standard operating procedure for most merchants for decades. Indeed, they are a natural outcome of having products where demand outstrips supply (either delivery from another vendor or in-house manufacturing capabilities). When inventory ran out, the merchant would take a backorder and the customer would simply have to wait for the item to be in stock again.
This procedure doesn’t work in today’s digital economy, however. Today’s consumer is used to a higher standard of service, brought on by the promises of Amazon and other large internet retailers. This higher standard includes order processing within 24 hours, prompt shipping, and speedy delivery at a low cost. Needless to say, consumers with these expectations do not tolerate backorders.
Even more problematic is deciding what to do when the inventory actually comes in and it is time to fulfill those backorders. Here’s the issue: suppose you choose to ship it to the customer. He or she might accept it—then again, he or she might not want the item(s) anymore. In this case, the customer will refuse the order, leaving you on the hook for the delivery fee (and having to issue a refund).
Things are even more complicated if a customer orders multiple items at once. Do you wait for the back ordered item to come in before sending a shipment? If so, you might have to deal with multiple returns by the time the customer gets the shipment. Or do you send each item as it becomes available? That’s a better solution, but it means way more in terms of shipping costs—shipping costs that you, the vendor, will have to absorb.
Avoiding backorders doesn’t just make your customers happier; it positively affects your bottom line, too.
If you'd like to find out more about inventory tracking and optimization, feel free to reach out.