How to Label Warehouse Racking and Shelving for Maximum Efficiency
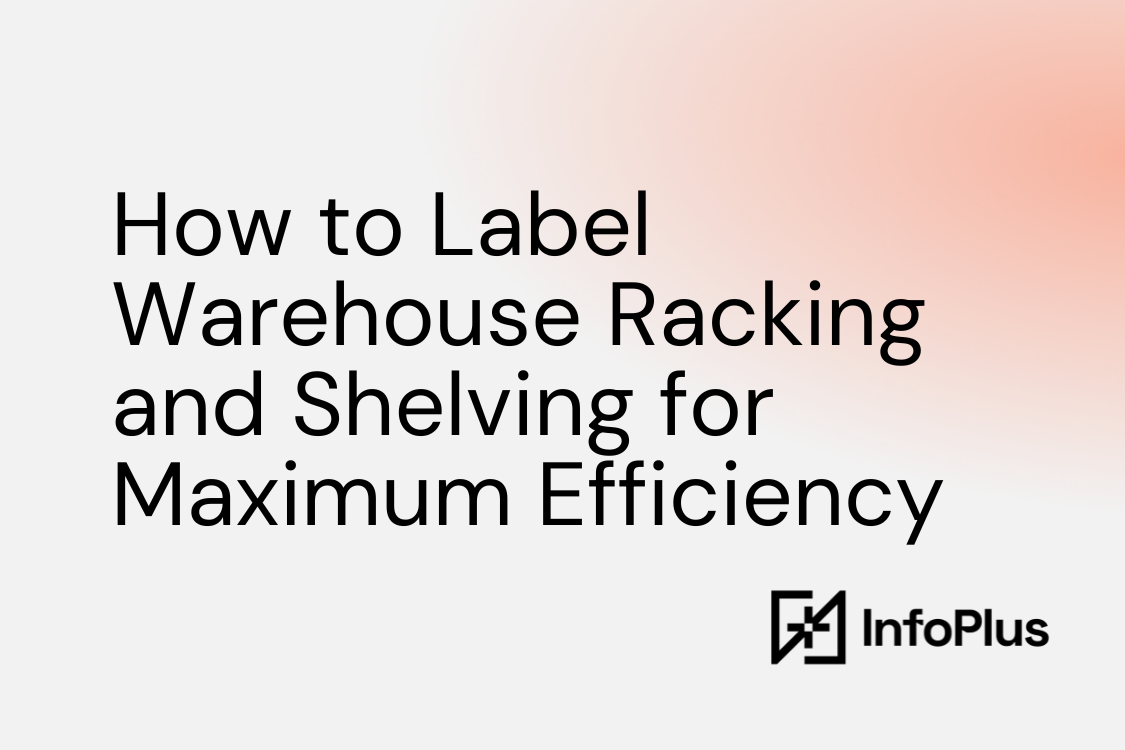
Labeling warehouse racks might seem like a minor detail. But if you’ve ever been to a large grocery store or hardware store that lacked proper labeling, its importance becomes obvious. Paying a little attention to proper rack labeling and addressing will lead to big payoffs in picking time and overall warehouse efficiency.
The perfect time to make decisions about your rack labeling is when you are engaged in your warehouse setup. After all, setup is when you’ll pay careful attention to how your warehouse operates. Think of it this way: your warehouse layout is the roadmap. The labels are the road signs that help your employees navigate it.
The best way to create an address system and begin labeling focuses on optimal pick paths. Your layout and labels need to create a direct line from point A to point B with workers taking the shortest routes possible. With the right labeling method, you’ll see efficiency. Without it, get ready for the chaos.
What Does Good Warehouse Labeling Look Like?
The ideal label address includes precise information that describes an item’s location. It starts by naming the largest area and drills down to the smallest.
Think about how the post office sorts mail. There are millions of addresses, but your mail carrier manages to get your mail into your mailbox (at least most of the time!). This reliability is all thanks to a proven method of using unique addresses.
At the post office, items are first sorted by state, then by zip code. The city follows, then the street, and finally, the street number.
A warehouse storage area should be organized and labeled in the same way, except they will reference things like a SKUs aisle, bay, level, and bin. Let’s look at an example:
- Our storage area has three aisles. We’ll number those 1, 2, and 3.
- Along each aisle are six bays (sections of shelving). Those will be numbered 01 through 06.
- Each bay has three levels. We’ll call the ground level A, the middle B, and the top C.
- And each bay holds four bins. We’ll number those 01 through 04.
Any item on any shelf has its own unique address. If the pick-slip reads 2-01-B-03, we know that in aisle 2, in the first bay, we’ll find the item in the third bin on the middle shelf. (Notice how the use of alternating one- and two-digit numbers and letters makes the address easier to read.)
How to Label Warehouse Racks: The 7 Components of an Effective Warehouse Location Address
Whether your warehouse is automated or uses paper pick-tickets, the unique address will tell stockers and pickers exactly where items are. Any successful warehouse address system follows these principles:
- The system must be sequential. Labels should use a combination of numbers and letters in sequential order to identify the exact location on the rack. It wouldn’t make sense to use some other descriptor. For example, if you used a color, there would be no intuitive way to determine the order. Would blue come before green? Or vice versa? The answer would be arbitrary and not obvious.
- Alternate the use of numbers and letters. In our example above, the levels were labeled with letters. We used single digits for the aisles and double digits for the bays. Variations like this will make longer strings of numbers easier to read and reduce transposition errors.
- The numbering system must be user-intuitive. It must make logical sense to the warehouse employees who will use it every day. This goes for people stocking incoming products on the shelves, workers taking inventory, and those picking items for shipping.
- Labels should be easy to find and read. The address must be easy to see and understand in a fast-paced warehouse environment. If you’re dealing with multi-level shelving, put all the labels at eye-level. Some systems use arrows to indicate the level. A side- or down-pointing arrow means the lower level; an upward-pointing arrow indicates the next level, and two upward-pointing arrows the level about that, and so on.
- Be consistent. Stick to a uniform location for placing the label on a rack. Having some on the left side and others on the right, for example, will be confusing.
- Addresses on labels should be the same as those used in pick path plans. Ideally, you should use the same warehouse management software (WMS) both to generate your labels and plan your pick paths to ensure consistency. You can use our free online tool to generate barcodes, to get you started.
- Use the right label materials. Labels can be adhesive stickers, magnets, or metal labels. Your choice depends on your budget and how much flexibility you want. For example, paper stickers can be printed more quickly and inexpensively than metal labels, allowing for easy changes in inventory. On the other hand, metal ones last longer and withstand more abuse. If extreme temperatures or humidity come into play, you might opt for magnetic labels over adhesive stickers.
The down-forward picking area, which typically contains the items needed to process a day’s worth of orders, needs a labeling system, too. It can use a different numbering method than the bulk storage area, but the same rules apply regarding sequencing, alternating, and logic.
Proper Storage in a Racking System
Your warehouse storage should already be set up based on your pick paths. We use the analogy of a highway to describe an active warehouse. The space must be designed to allow people, products, and machinery to travel smoothly. Cross traffic, backtracking, bottlenecks, and collisions should be avoided at all costs.
Using predictive analytics, you know the velocity of your products. In your storage area, common items are conveniently located in easy-to-reach spots. Backup inventory or seldom-ordered items are on higher racks or further away from the down-forward picking area. The down-forward picking area is reserved for units that will be picked and packed right away. This area is replenished frequently. (We discuss the best way to set up your storage area in our Warehouse Set-Up 101 articles for small, medium, and large warehouses.)
Pick Paths and Pick Sequencing
So what do pick paths have to do with how to label shelves in a warehouse? In a word: Everything.
Smart pick sequencing accounts for pick paths as it directs pickers through the space. The labels are their signposts. Again, the goal is to have employees traveling the shortest, most efficient route to collect the items on their pick ticket.
When organizing your pick sequencing for optimal flow and efficiency, you should consider the following:
- Pick sequences should have pickers traveling down the aisles in one direction when possible. Going back and forth wastes steps and can put employees in each other’s way. So here’s an idea: have even numbers on one side of the aisle and odd numbers on the other. This way pickers will immediately know which side of the aisle to focus on. They’ll get used to weaving from side to side as they go down the aisle.
- A pick sequence should group together items that are located near one another on the shelves, or on the same path. It doesn’t make sense to pick three items from aisle 1 and three items from aisle 2, then go back and pick two from aisle 1 and four from aisle 2 on the next ticket. That’s picking 101.
- Keep in mind the method of picking. If you have some items collected on foot with a cart, they shouldn’t be in the same pick sequence as pallets requiring a forklift.
- The physical layout of your shelving needs to provide for the type of traffic that occurs. Is there room for two people, carts, or forklifts to pass each other if they need to? If not, you need to rethink your storage space or your pick path.
As with any changes you make to your warehouse, it’s crucial to complete a dry run of any new warehouse concept you adopt. The same goes for your labeling system. Think ahead to how you expect your business to grow or change and make sure you can modify your plan if and when things change.
Part of this is ensuring that you have a robust warehouse management system that can keep track of inventory and generate pick tickets consistent with a labeling system that employs these best practices. We’ve built just such a labeling system into Infoplus Commerce, and many other tools as well. If you would like to see a demo of Infoplus in action, reach out to us and we’ll put you in touch with our experts.