Elimination of Mis-Picks Results in Advantages Today and in The Future
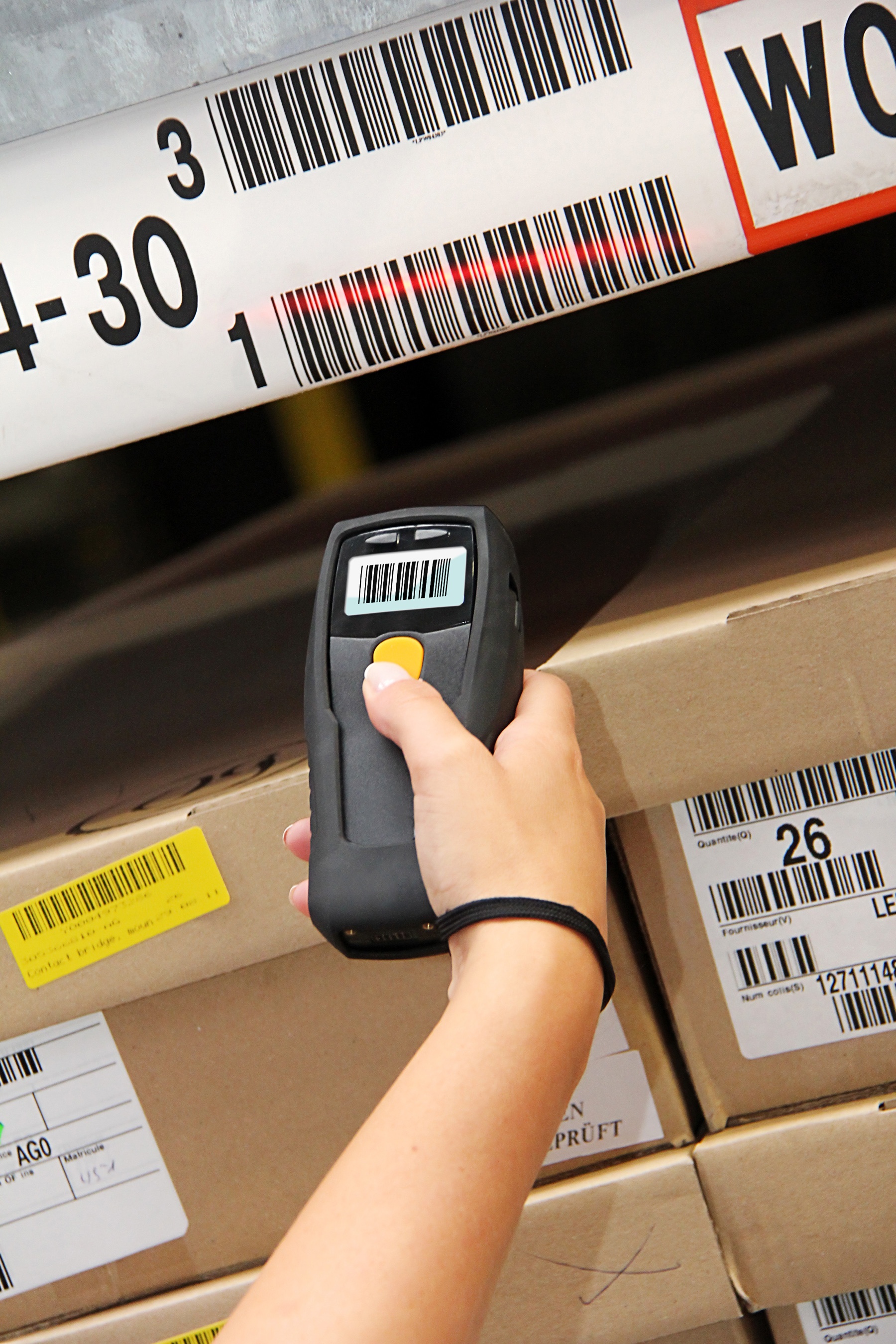
Mis-picks in an order fulfillment operation can cause far greater problems than merely wasteful task repetition on the warehouse floor. Both company-sanctioned and independent websites offer customers opportunities to voice their opinions on just about anything these days...including the accuracy and timeliness of an order. It’s “shipper beware.”
Why Retailers Could Get Away With Mis-Picks in a Pre-Digital World
In the not-too-distant past, shipping the wrong product from a warehouse to a customer had few ramifications. At worst, you and your company had the added cost from processing the order a second (and unnecessary) time, the extra shipping cost itself, and the loss, in wholesale cost, of the original, mis-picked item, which oftentimes wouldn’t be returned by the often-irate customer.
At best, you didn’t hear anything. Sure, the customer might possibly seek out an alternative product, but you didn’t know about it. And the resulting negative reflection on the bottom line was noticed only by those at the top who pay attention to such things. Of course, a noticeable dip in the sales curve due to too many such mistakes begins to get noticed. And when management traces these mistakes to the fulfillment department…suddenly that negative reflection is on YOU.
The internet has changed this. The idea of an unhappy customer suffering in silence is now history—and has been for approximately two decades now. So while mis-picks and packing errors were certainly always something to be avoided due to the short-term logistical and/or cost consequences, such mistakes can now have long-term brand image effects.
Yes, you’ll hear from the unhappy customer. But so will the rest of the world, via social media, direct mass emails, or online review sites. It’s for all of these reasons that you minimize, if not eliminate, mis-picks. Thankfully, a good warehouse management software makes it nearly impossible to pick the wrong item for shipping.
Minimal Mis-Picks, Maximum Efficiency
Newer WMS works with any scan gun to ensure accurate picks, while streamlining your overall warehouse operation—including inventory, orders, and shipment—with optimum efficiency and in real time.
Additionally, a number of benefits that contribute to maximizing efficiency while reducing mis-picks:
- Location Scanning makes it possible to assign locations to inventory in order to enable greater tracking and the ability to store product randomly, rather than by ID number, vendor, product description, etc. Space utilization is increased by slotting your product in a way that matches the physical characteristics of a storage location to those of the specific product. You can also increase productivity by locating fast-moving product to closer, more accessible locations and increase accuracy by separating similar items.
- Scan-to-Cart Methodology, or Pick to Cart, allows an operator to scan items for a batch of orders into LPNs on a picking cart, laid out by order, adding an additional layer of quality control to the picking process. This eliminates the need for a sorting station and ensures fast mobile pick and shipment confirmation. This can be accomplished by a single person, reducing labor.
- Seamless Order Transfer moves orders digitally from station to station, minimizing what floor workers have to write down. This means fewer opportunities for errors and easier instructions for everyone.
- Weight Verification is a pioneering technology that gives operators the ability to confirm a correct pick by weight of the product (which would already be known by the system) to further ensure accurate shipping.
In any warehouse or fulfillment operation, labor is the single biggest expense. You will want to make sure you are getting the most out of it, optimizing each activity performed. With that level of detail needed, modern software solutions are the way to go.