You Might Be Choosing Warehouse Management Software For All The Wrong Reasons
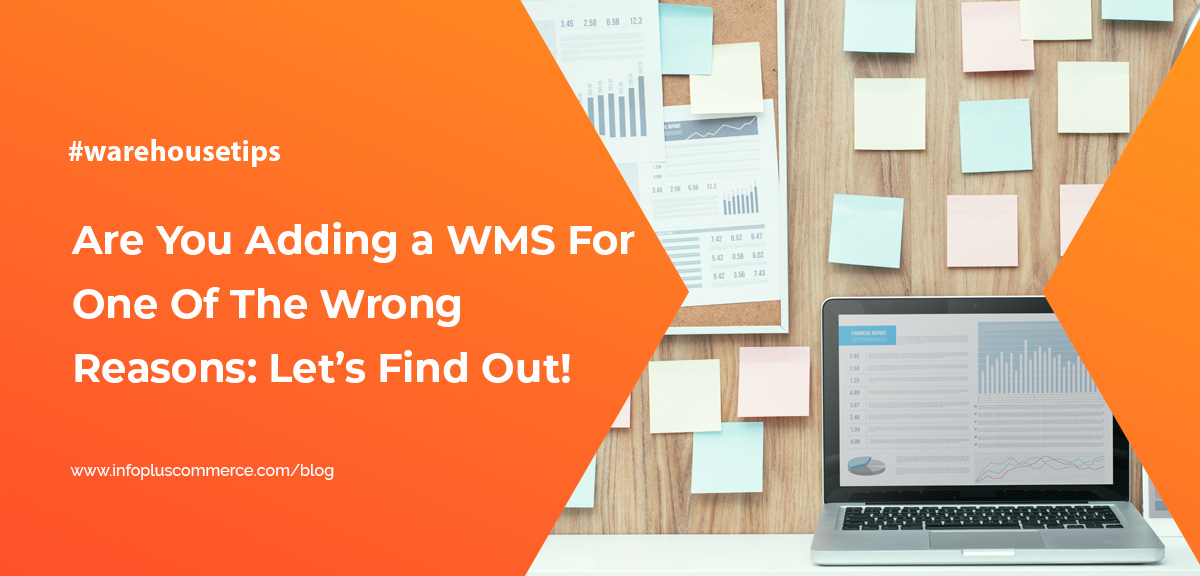
A Warehouse Management Software is a powerful tool—but it’s not the answer to every warehouse’s prayers. So what is the best way to determine what solutions will work? And how do you know when Warehouse Management Software is the answer? The answer lies in examining every aspect of the warehouse to get to the heart of the problem.
WMS should never be considered a panacea or a magic bullet. If the processes established in a warehouse are flawed, no amount of technology will fix them.
Are you adding a WMS for one of the wrong reasons? Let’s find out.
Getting a Warehouse Management Software Band-aid, Not a Warehouse Health Checkup
We like to compare crises or challenges in a warehouse to an illness or injury. Too often, individuals want to slap a band-aid on a health problem instead of going to the doctor to find out the underlying problem.
Sure, the patient might get lucky and a band-aid is a perfect remedy (especially if that patient is a two-year-old). But usually, there’s something else going on. The perceived problem might only be a symptom of a much more serious issue. Only by examining the bigger picture can the true source of the problem be diagnosed and a proper course of action taken.
For example, if disorganized shelving in a warehouse makes it hard to find things and fill orders, the warehouse manager might want to buy a cloud based Warehouse Management Software (WMS) to automatically print barcode labels. This might improve things somewhat, but it’s really just a band-aid. The health-check approach would be to re-examine the entire shelving process: How often are things shelved? Is inventory grouped and organized according to velocity? Is the forward-picking area being used appropriately?
Not Envisioning the Ideal Warehouse
In a warehouse environment, we see numerous instances of this type of tunnel vision when it comes to warehouse management software. WMS is often the band-aid that will “save the day” when something goes wrong.
When a challenge arises, a warehouse manager might decide to fix the problem by finding a WMS with a feature to address that specific problem. On the surface, there’s nothing wrong with that. But it’s counterproductive to implement a solution for problems in processes Y and Z, without first looking at what’s happening in processes A through X.
As we’ve discussed in all of our other articles about warehouse design, all of the processes in a warehouse are interconnected. Efficiency in the receiving area contributes to an organized storage area; effective picking methods lead to correct order fulfillment, and so on.
Bad processes are bad processes—period. Relying on WMS alone to fix them is unrealistic and a waste of time and money. It’s like expecting to get in shape simply by purchasing a new piece of exercise equipment without using it regularly and examining your diet and lifestyle.
Instead of rushing to buy a Warehouse Management Software to address a problem, managers must look at the situation as an opportunity to reinvestigate the processes they have in place. It is a time to re-envision what their ideal operation would look like. Armed with this insight, the decisions they make will fix problems without blowing the budget on the wrong solutions.
Solving the Wrong Problems With a WMS
If a patient has a broken arm, there’s absolutely nothing a band-aid can do. A problem in warehouse procedures never looks this obvious, but we see similar mistakes being made.
Let’s take the example of a company experiencing a sudden increase in customer returns. A manager might decide to fix the problem by finding warehouse management software with a feature to handle the high volume of returns piling up. A new system is implemented to receive returns, send them back to the manufacturer, and ship a replacement to the customer.
Meanwhile, no one has bothered to investigate further: why have returns increased? If customers are receiving incorrect items, then there could be a problem with your order picking method, inconsistencies in labeling in the storage area, or a lack of verifying orders before they are packed for shipping.
If products are returned because of damage, where is the damage is happening? Perhaps the shipping carrier mishandles fragile items. Or maybe damaged goods wind up in storage because of inadequate quality control in the receiving area.
The new cloud based warehouse management software can handle what happens to returned items, but it won’t solve the root problem. Pinpointing exactly what went wrong will, in turn, reveal an appropriate solution. The manager must take a step back and examine the entire warehouse process to know they are solving the right problem.
Falling in Love With the “Bells and Whistles” of Warehouse Management Software
In short, a warehouse manager should spend time diagnosing and solving real problems, not just surface symptoms. And he or she should look at tools to solve those problems, not just technology with shiny new features.
We see it all the time: A warehouse manager falls in love with an idea and then runs out to shop for a software solution that has a particular feature without thinking clearly about the warehouse systems involved. How many times have you heard these features being discussed as the “hot new thing” that warehouses need?
- Mobile compatibility
- Big data/analytics
- Real-time updates/counts
- Omni-channel
- Labor management
Don’t be mistaken: These are all useful tools, and they make sense in the right context. The problem is that people ask for them without thinking about whether they need them and how they need to be set up.
It can also be true that a Warehouse Management Software might be part, but not all, of the solution. For example, it might create improved pick paths, but if you don’t have a forward picking area, there’s only so much it can do. Or software may solve a number of quality control issues, but it can’t change the fact that your receiving area is too small.
Investing in software with more bells and whistles than necessary can be detrimental in several ways. First, it’s expensive. Not only is there the initial cost for the software package but also the time spent training employees to use it. Once the software is up and running, it could cost more in productivity and efficiency by adding additional steps to procedures in order to accommodate the software’s requirements. The unintended result could be a less efficient warehouse.
A manager is better off looking for solutions that fit warehouse operations. That might mean a less expensive, stand-alone software instead of an entire comprehensive warehouse management system. In some cases, it might even mean forgoing new software entirely. For example, additional training might improve quality control results. Or, if a warehouse is operating at top efficiency with a manual labeling system, why spend the money for barcode printers and readers?
Again, simply doing a feature hunt will end up costing you much more in the long run than simply taking a look at your entire warehouse process.
The Solution: Choose Assessment Before Investment
Instead of applying band-aids in the form of warehouse management software, managers must first stop and ask themselves if it will improve the overall productivity in the warehouse.
Warehouse Management Software is a significant investment. Before purchasing, you should perform a thorough health checkup of warehouse operations. You could even hire a warehouse consultant to help. Once you drill down, you will uncover hidden flaws in the processes and learn exactly what problems you need to fix. The time and money spent to assess the warehouse’s overall health will be well worth it.