How to Run a Warehouse Health Check?
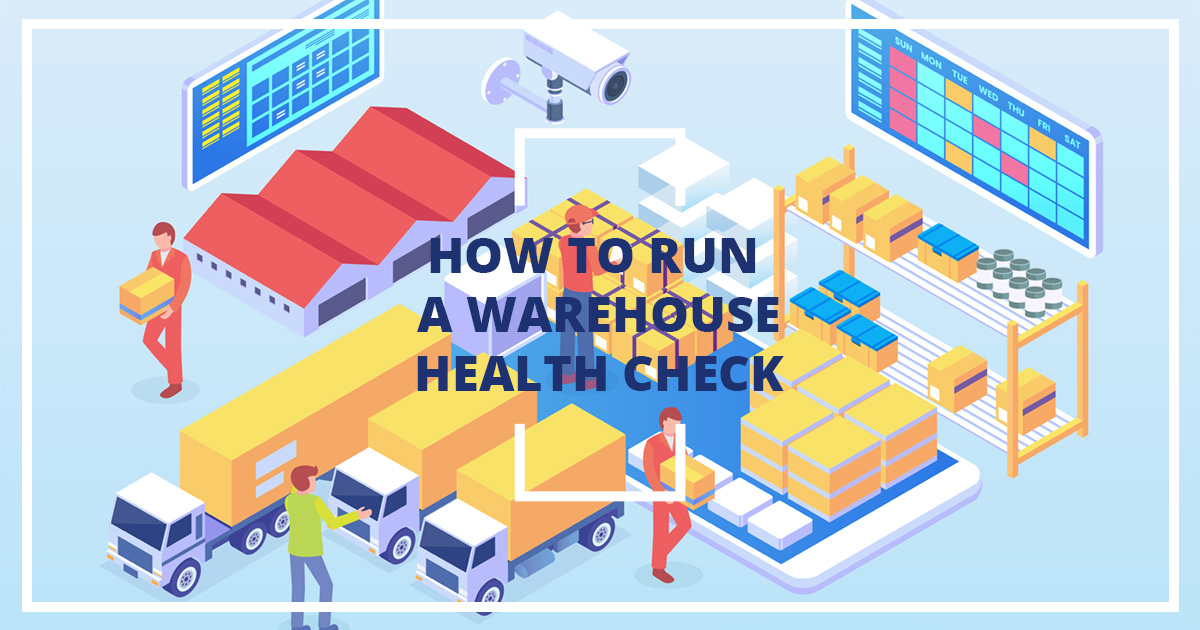
Is your warehouse profitable, or is it a major cost center for your organization? Is it running as efficiently as possible, or are there key areas that need some careful attention? Simply put, is your warehouse healthy or not? If you’re unsure about the answers to these questions, it’s time to perform a warehouse health check.
The idea behind a warehouse health check is to step away from the day-to-day operations and assess whether the warehouse is helping or hurting your most critical business operations. If there’s a problem, the health check should help you diagnose what exactly that problem is.
Here is our 4 step formula for conducting a focused, effective warehouse health check:
1) Pick the Right Warehouse KPIs
Different warehouse KPIs (key performance indicators ) will be more or less helpful depending on your industry and business model. For example, if you have an e-commerce warehouse and your business has an SLA promising shipping within 24 hours, order lead time might be the top KPI you need to track. If you handle several delicate luxury items, warehouse KPIs like order damage, rate of returns, and total cost of storage are more important for your warehouse.
Your business strategy also affects your warehouse KPI choice. If aggressive growth is the plan, you must watch your back-order rate and transportation cost per package. If you are simply interested in making your warehouse profitable, carrying the cost of inventory and sales-to-inventory ratio might give you a better picture of your warehouse’s overall health.
There are twenty KPIs you could choose from. But we recommend finding only a handful (four or five) to get the snapshot you need of your warehouse operations.
2) Find Out the Industry Averages for Your Business
Have you selected your warehouse KPIs (Different key performance indicators)? Good. Hopefully, you have a plan for collecting this data and presenting it, too.
But remember: warehouse KPIs are just numbers on a page until you know what they mean. For example, if your rate of returns in your is 4%, is that a good thing? Or does it point to a problem?
You can’t tell until you have a feel for what’s typical for your industry. Consider that 4% rate of returns. If you run an eCommerce clothing store, that number is fantastic, because the average rate of returns for clothing is very high. (Duh—people will buy on impulse but just as quickly return a shirt that doesn’t fit or look right in the mirror.) But if you have a 4% rate of return for physical books, hand tools, or consumer electronics...well, you might have a problem.
When finding averages for these KPIs, it helps to find the median average, not the mean. “Median” means the middle value; if the median order lead time is three business days, then half of the organizations in your industry will have an order lead time that is equal or better to three, and half will have an order lead time that is worse.
Why use the median and not the mean? (The “mean” average is the average we learned in grade school, where you add all values together and divide by the number of reports). The problem with the industry’s mean is that a few powerhouses can throw off the average. For example, Amazon, Walmart, and Target might have order lead times around three hours, while everyone else takes a day or more… but the overall average or mean would still come out well under one day!
All told, the median is a fairer benchmark than the mean.
How can you find out industry averages for your chosen KPIs? First, try combing industry-specific publications. Independent researchers will, from time to time, share relevant industry averages. And today’s search engines help you to find what you are looking for in a short amount of time. You might not find all your KPIs this way, but you will find the most critical KPI’s to use them as a starting point.
Second, turn to your vendors, especially vendors involved in any aspect of warehouse management and support. It’s entirely possible that they have some statistics based on their own pool of customers. They probably can’t share details, but they might share averages—which is really all you need.
3) See How You Measure Up
Now the rubber meets the road: How does your warehouse compare to the industry averages? If you’re at the average, that’s fine—it means that, while there is room for improvement, you aren’t worse off than most. However, if you are below the average, you probably aren’t following all the best practices for your industry.
Getting a single snapshot view of your KPIs against the industry average is fine for doing a warehouse health check. But keep in mind that you will want to track these KPIs over time and look for movement. Is your rate of returns dropping as you implement new processes and quality controls? Is your carrying cost of inventory dropping as you get a more efficient set-up and renegotiate lease rates? Remember, these are all measures of a dynamic, changing warehouse, and you’ll want to notice patterns in their movement, too.
4) Identify Problems and Work Backward
When you have done the above procedure, you’ll find there are some measures are off. Now it’s time to do something about them!
The plan should be to work your way backward, from shipping all the way back to receiving, to see what your bottlenecks and problem areas are. To do this, you’ll need a precise way to track inventory through the warehouse. This will allow you to get more precise KPIs for each stage of your storage and fulfillment processes.
For example, let’s say your order damage KPI is too high; roughly 3% of orders are being returned or reported damaged. Start with your shipping and packing area: Are items being quality-control-checked for breakage? If not, start doing that. Is the filler material appropriate to protect items while in transit? Are machines (or people) handling orders too roughly during packing and shipping?
Once you feel you’ve addressed each of these issues, check your KPI. Has it improved? If so, great! Time to look for the next bottleneck. If not, then take the process back a step.
Back to the order damage example: If order damage rates are still high even after overhauling the shipping area, move to picking. Are pickers doing a quality control pick as they go? If not, should they? Are they using the right handling and transportation equipment? Are items shelved appropriately to avoid damage or spoilage—for example, are heavier items closer to the floor?
Again, once you are satisfied that damage is not a result of picking, move to storage. Are items being shelved carefully? Are they being protected from pests, temperature extremes, and so on? Correct any of these issues before moving on.
Finally, look at your receiving area. Are dock workers doing the appropriate quality checks once they receive goods? If items are coming from your supplier damaged, you need to contact them and get this resolved! Next, are damaged items being stored with good items instead of being held in their own separate area? Are undamaged goods somehow being damaged when picked up for storage? These questions need to be addressed, too.
We’ve used the example of order damage because it’s easy to visualize. With a little creativity, though, you can see how this process works for other KPIs. Take order lead time, for instance. If orders are slow getting out the door, where is the bottleneck? Is it in preparing packages for shipping? In packing items into shipping containers? In moving items to and from forward staging? In pickers following their pick paths? Something, somewhere, causes the bottleneck. The point of the warehouse health check is to determine where such bottlenecks might be hiding.
Need Help with Your Warehouse Health Check?
Sometimes your leadership might have trouble agreeing on the appropriate KPIs to use. Or you might have the right KPIs for your warehouse but no idea what the industry averages are. Or you might know the averages and know you fall short, but you can’t figure out how to locate the problem in your warehouse.
If you want help with your own warehouse health check, just reach out to us. Here at Infoplus, we’ve helped many warehouse managers with their assessments, setting them up for further success. Or you can learn more by checking out our other articles and learning epics.