Warehouse Technology, Operations, and Inventory Management
Featured Posts
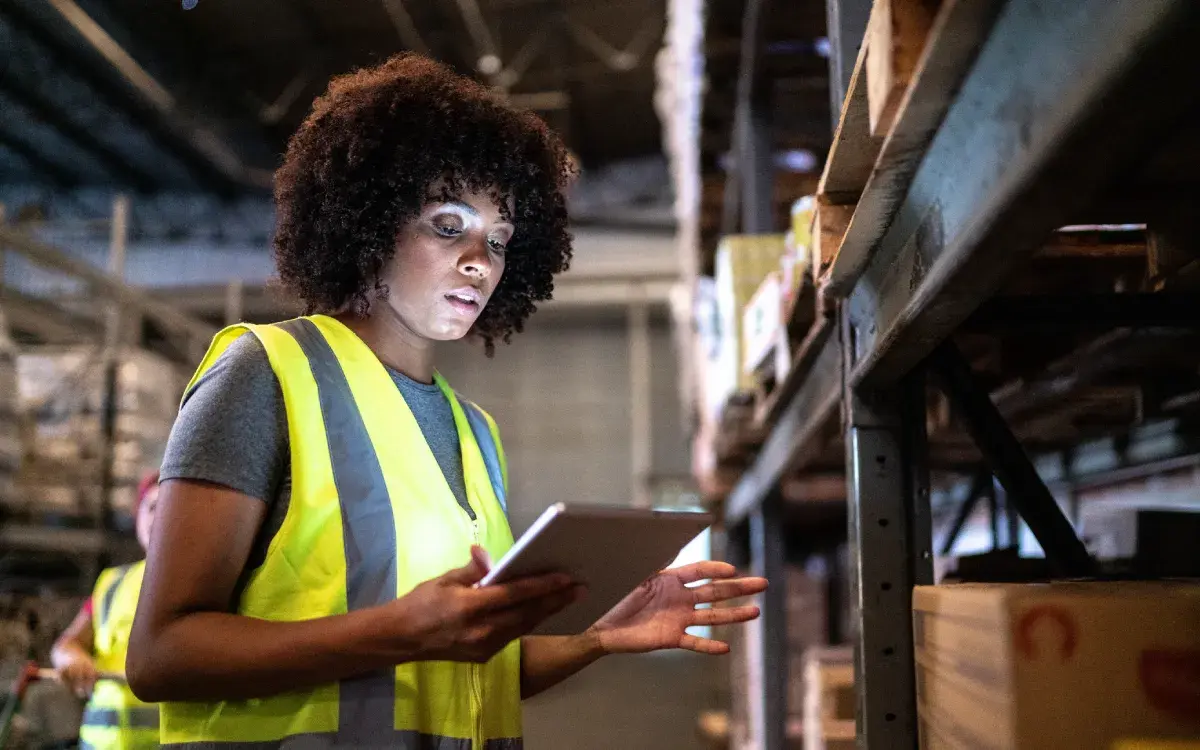
February 28, 2024
Demystifying Fulfillment Management Software
In the ever-changing world of warehouse management, it's easy to feel lost in a sea of industry jargon and buzzwords. One such term gaining attention...