12 Warning Signs of a Bad Warehouse Layout - Updated
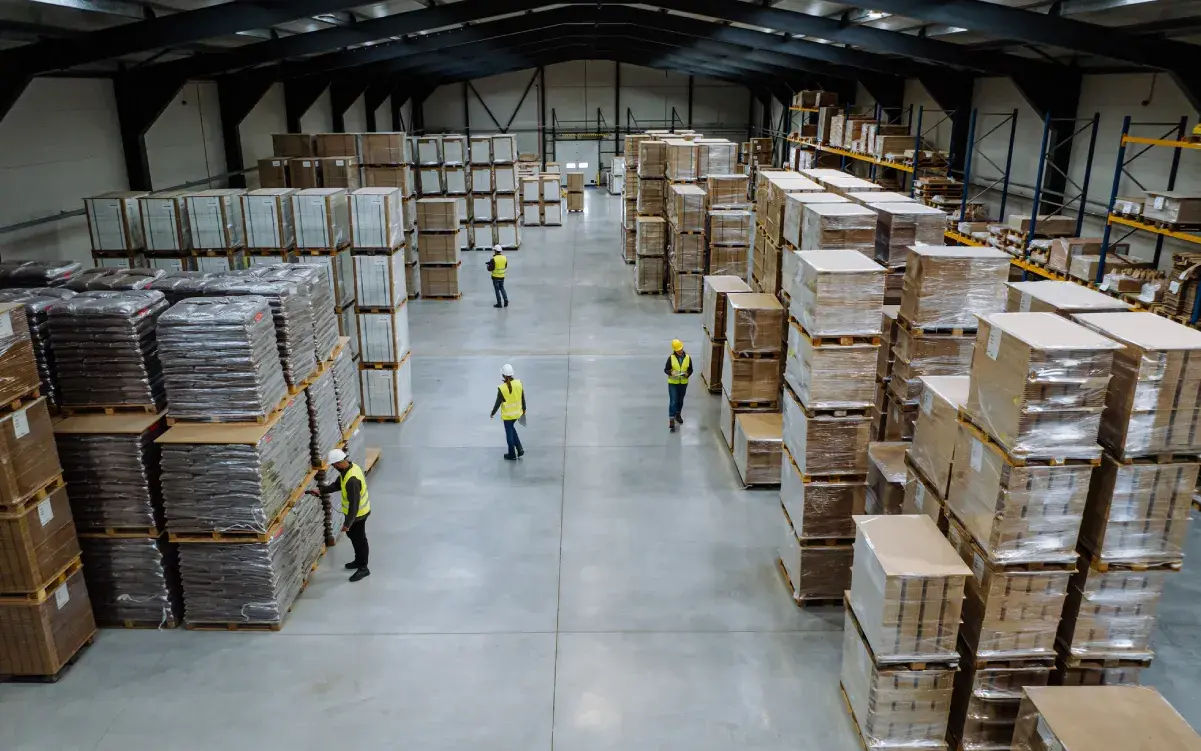
If you are a warehouse manager, you must be open to the possibility that a faulty warehouse layout could be at the core of the inefficiencies you are seeing. Here are 12 warning signs of a bad warehouse layout and setup.
When you notice a lack of efficiency or order fulfillment issues, that doesn’t always mean you have a bad warehouse layout problem, but it might. Sure, there could mitigating factors which immediately point your attention to vendors, equipment, employees, and so forth. While those areas might need improvement, the core problem may actually sit with how your warehouse is set up.
A faulty layout will impact the entire space, especially how people, machines, and materials facilitate order picking and shipping. Knowledgeable managers are always on the lookout for layout problems in the warehouse, too, as these are often at the root of workflow and process issues.
How do you know when you have a bad warehouse layout, and what common warehouse warning signs signal the need for layout improvements?
ONE: A Persistent Order Backlog
When teams are still working on Thursday to fulfill orders that should have shipped Monday, there’s a problem. Perhaps you have some training issues or you’re understaffed. However, make sure those workers are free to be as efficient as possible, with pick paths that have them traveling the shortest distance possible, and inventory organized into zones improve picking efficiency.
TWO: Large and Heavy Items Lingering Near Receiving
If you have insufficient shelving and aisle space, your personnel may find it harder to to shelve large, heavy items. Those heavy items more often than not, end up on the floor. Those oversized or heavy items being stashed in the wrong place is a clear sign you have a bad warehouse layout. Clutter is both a safety concern and a common cause of traffic and bottlenecks.
THREE: A High Rate of Lost of Inventory
There will always be some loss of inventory due to breakage, spoilage, or more rarely, theft. But sudden spikes in lost inventory without a similar spike in orders (or damage, from an unfortunate event like a leaky roof during a storm) probably signal you have a faulty warehouse layout problem. A quick fix: Check to make sure your team is slotting and putting inventory is being put away promptly.
FOUR: Inadequate Forward Picking Space
It’s not just unlikely but impossible that every item in the warehouse sells at the same rate. If you don’t have enough forward picking area to accommodate high-velocity inventory or like items that sell together, those are two signals that your warehouse layout is faulty.
Instead: Set aside an area that's replenished daily with your high-velocity inventory and products that are typically sold together.
FIVE: Loading Dock Bottlenecks
A good warehouse layout should not have a shared shipping and receiving area, but it does happen. Those shared areas can eventually create a bottleneck at your loading dock, slowing both shipping and receiving. Instead, your dock should have separate areas with ample room for tasks such as packing and shipping, bundling, supplies storage, and labeling and addressing.
SIX: Dead Stock in the Aisles
“Dead stock” resulting from breakage, returns, or recalls must be assigned its own defined area until it can be returned to the vendor, thrown away, or inspected and reshelved. When dead stock sits in a random place, it not only will get in the way but could be mistaken by pickers for good inventory.
SEVEN: Your Pickers Can’t Locate Stock Efficiently
When pickers complain they can’t find or access items they need, you have an obvious warehouse warning sign: Either you have a problem with slotting, or with labeling your racks properly. Efficient slotting has been shown to save up to 20% in labor costs. Verify you have proper slotting procedures, and that you and the team are using clear rack labeling.
EIGHT: Safety and Collision Issues
When you see a high rate of Collisions and other warehouse accidents, those are a sign that you have a faulty warehouse layout. Accidents are inevitable, but a high collision rate probably isn’t the fault of your staff’s carelessness. When you don’t outline the correct pick paths, if your aisles are too narrow, or corners are too tight, crashes aren’t just likely. They’re inevitable.
NINE: Internal Transportation Cost KPI is High
When it comes to a bad warehouse layout, there are several KPIs to monitor. How much does it cost to move a piece of inventory from point A to point B? Locating something 10 feet away, instead of 50, can lower both the time and physical effort necessary to fulfill orders. A strategic layout can minimize these KPIs.
TEN: Orders Picked Per Hour KPI Has Plateaued
Human beings can only do so much with what you provide them. When you fail to improve the critical metric of orders picked per hour, your staff might simply have reached the maximum potential of what human beings can do within your warehouse layout. First, try adjusting picking methods and make sure to fully utilize forward picking areas, then monitor that metric to look for improvements.
ELEVEN: Monitor Your Average Days Late Metric
When seasonal spikes or insufficient staffing impact your efficiency, that resolves with time. But when you don’t see improvement, that could signal inefficient or bad warehouse layout. First, try to determine if the issue is isolated to just a few SKUs that are impacting your average—or whether you have a wider issue on your hands. Adjusting your warehouse layout could help with flow and improve your overall efficiency.
TWELVE: Inadequate Space for Growth and Overflow
Businesses evolve and change over time, and maybe you’ve simply outgrown your facility. That said, a common oversight in bad warehouse layout is a lack of planning for future growth and expansion. Try to first make the most of your existing square footage by creating an efficient flow of people and products. Be sure to use taller shelving and equipment that makes the most of vertical space as well as floor space.
Take The Next Steps to Improve a Bad Warehouse Layout
If you have observed any of those metrics or issues in your warehouse, here are some tips to get you back on the right track.
- Address the root issue. Following key performance indicators provides a wealth of data about all aspects of your warehouse operation. Using a WMS to define appropriate benchmarks and zero in on anything that falls short.
- Compare your layout to industry Best Practices. This might require looking at some sample layouts, or benchmarking your performance.
- Talk to the people working on the ground. Your warehouse staff and pickers can offer a first-hand view of what’s working, and what’s not. For example, are they walking too far to fulfill orders? Running into each other? Can’t find what they’re looking for? Data collection is great, but there’s nothing like human insight.
- Find the right solution for the right problem. While small problems usually only require a tweak here or there, systemic problems necessitate organizational changes.
- Be open to investing in steps 1-4. Diagnosing a bad warehouse layout problem requires software to gather real-time data and produce the right reports. Be ready to make an investment—here’s why.
Fixing the problem might mean investing in new shelving, equipment, or additional square footage. You also need a birds-eye view from a data and insight perspective for prescriptive changes that will make your warehouse staff both safer and more productive.
Warehouse management strategies, just like the rest of our dynamic industry, are constantly evolving. If you need to talk to an expert about investing in the right technology to improve your warehousing operations, contact us today and we can arrange a discussion with you and your team.